Inform online
Stories, trends and insights.
Our company magazine is exclusively created for our customers, partners and friends. Stay informed with the latest updates from our industry and company.
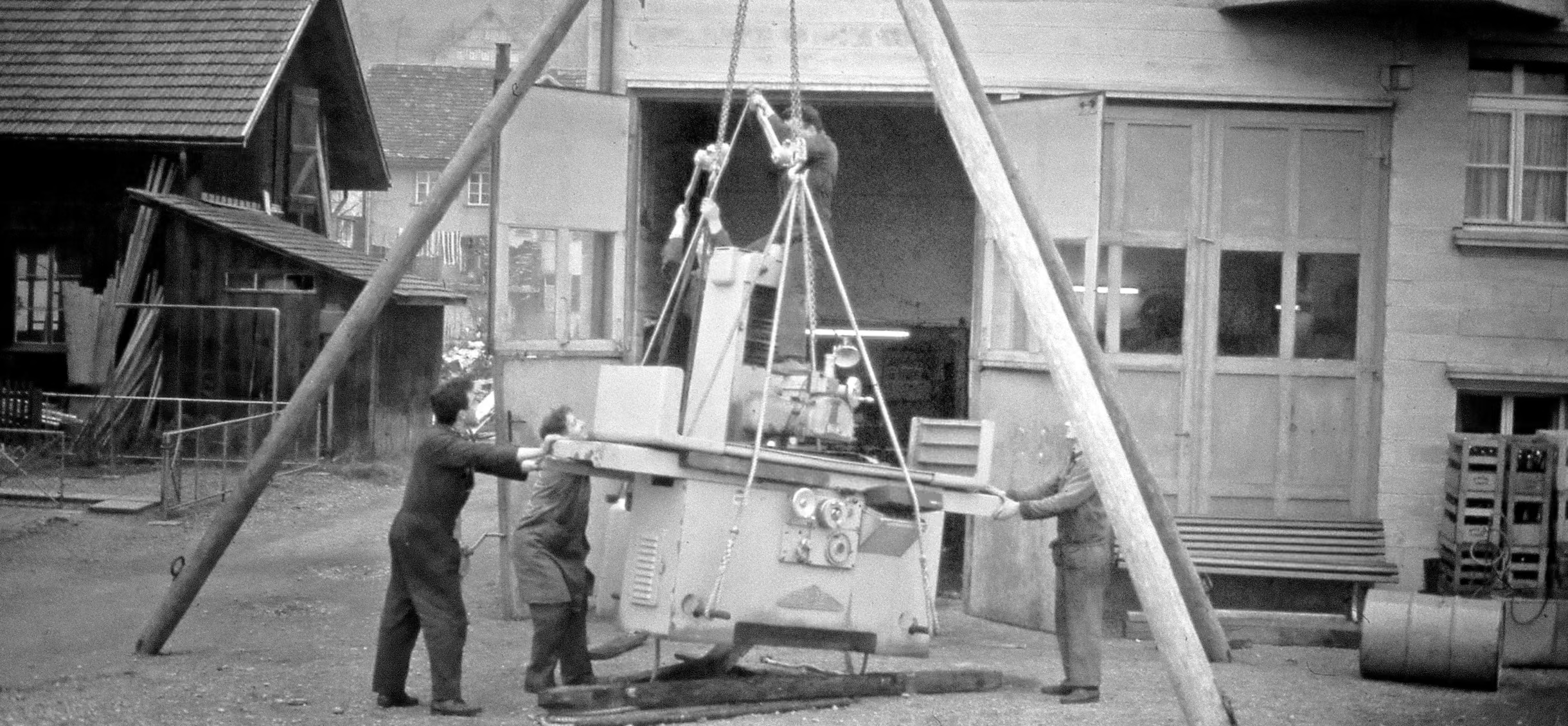
70 Years, precisely.
From its start-up in a small-town garage to its well-earned position as a global leader in the manufacture of high-precision injection moulds, Otto Hofstetter AG's journey goes back seven decades. It’s a story of bold innovation and unwavering determination. This Swiss family business continues to shape the industry today while remaining true to its roots and its core values. And the journey continues.
Overview of all blog posts.
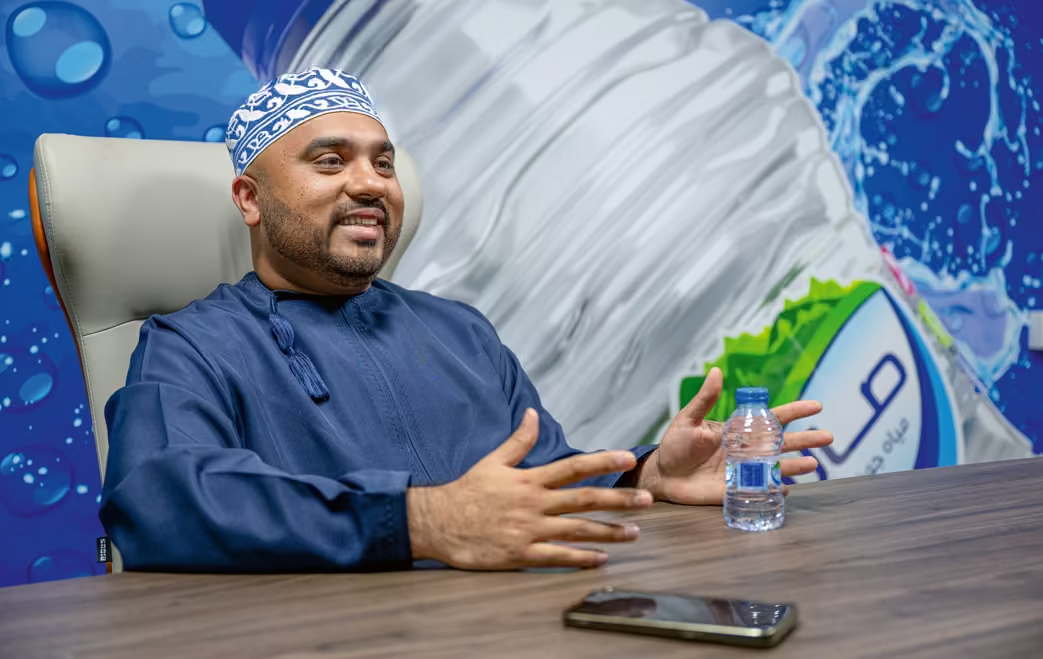
Set to lead.
In just two years, Sarooj Water has become Oman’s leading 250 ml water brand, driven by smart technology, local production, and a focus on quality and sustainability.
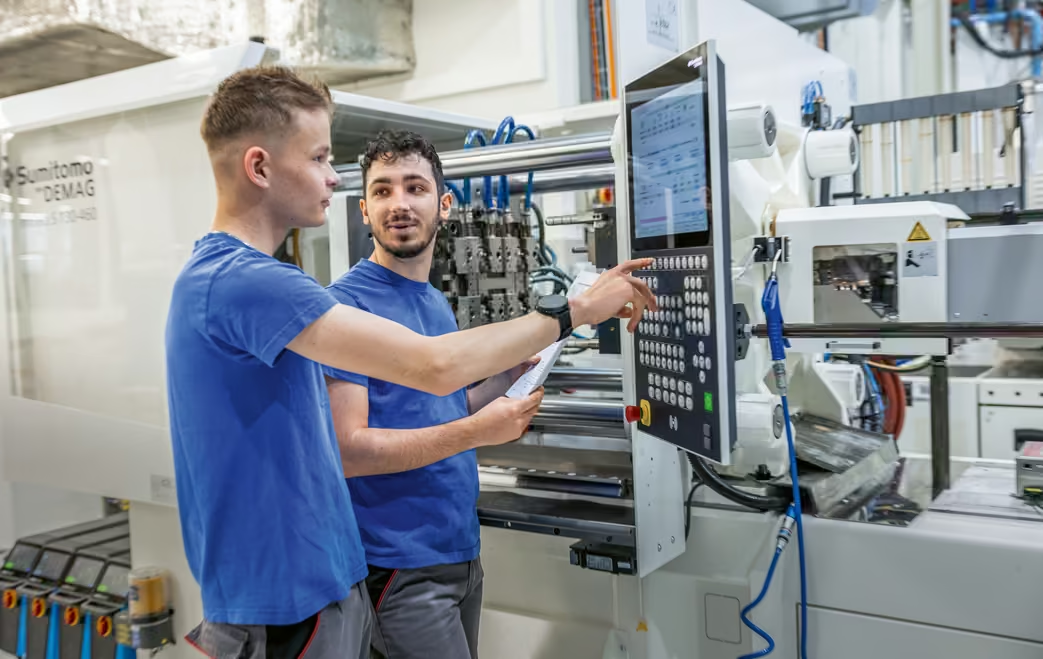
Job training with a vision.
Through hands-on training and strong industry ties, libs prepares Switzerland’s next generation of skilled workers — with Otto Hofstetter AG among its dedicated partners.
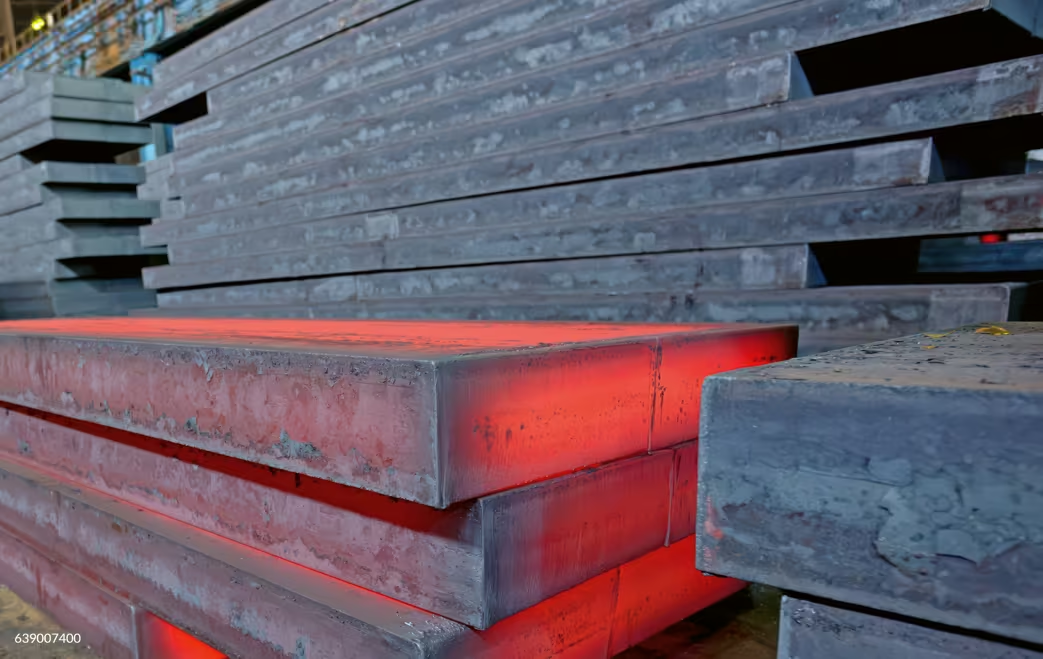
Steel going strong.
With specially developed steels and a focus on recycling, Otto Hofstetter AG enhances the durability and eco-footprint of its world-renowned injection moulds.
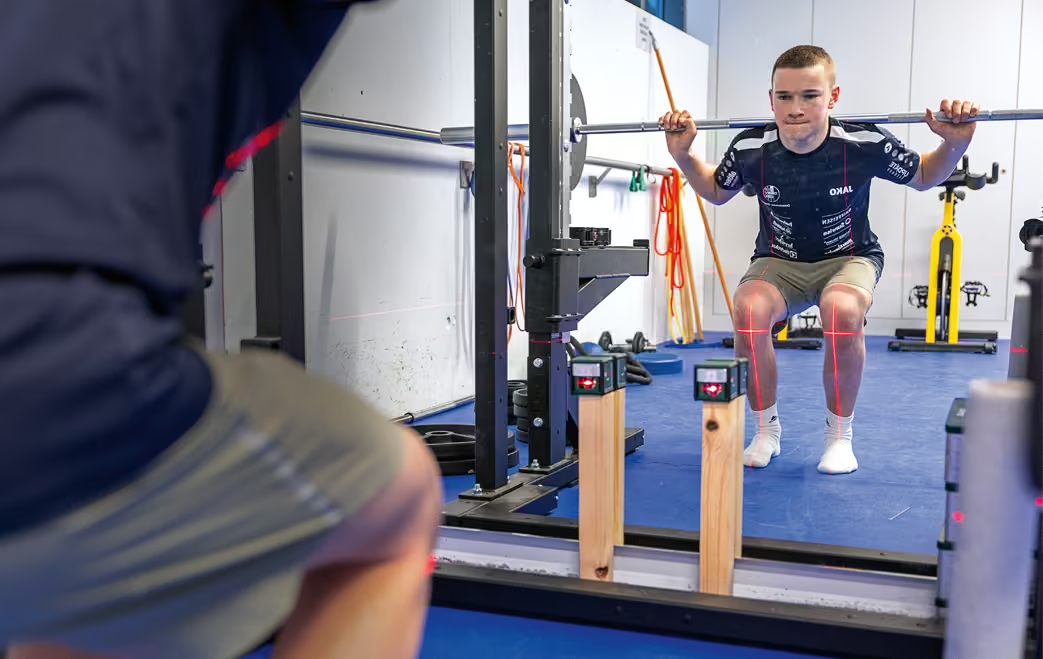
Precision wins.
Balancing top-level ski racing and technical training, Nick Zingg shows how discipline, precision, and planning lead to success both in sport and in his apprenticeship.
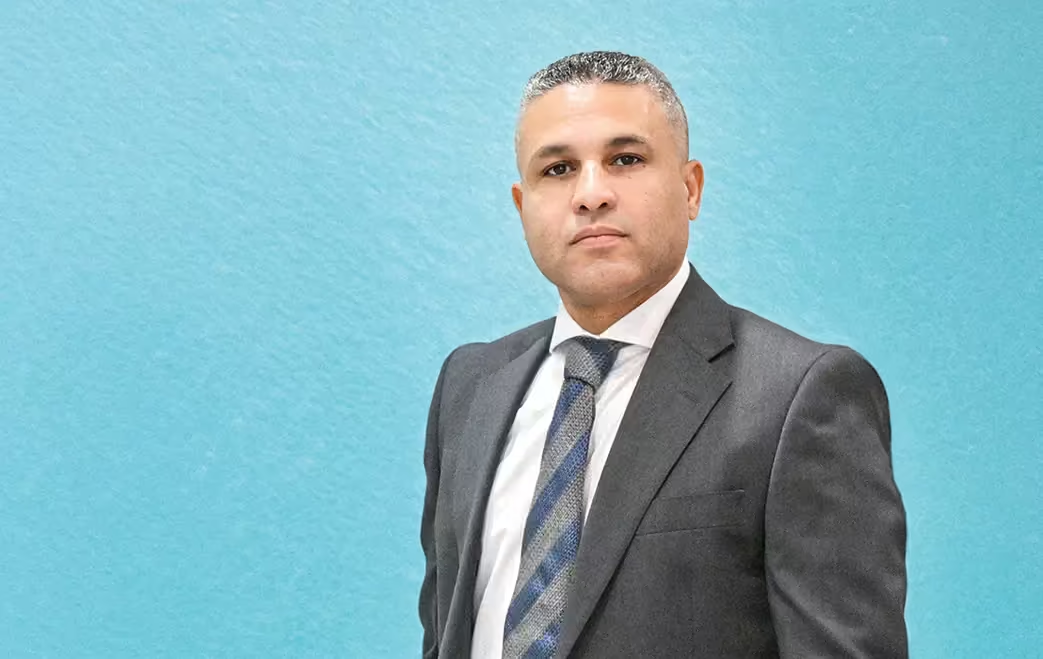
Superior sustainable quality and manufacturing excellence.
The Berain Water & Beverages Factory, a leading bottled water brand in Saudi Arabia, has its headquarters and two of its production facilities in Riyadh. A third plant is located in Jeddah.
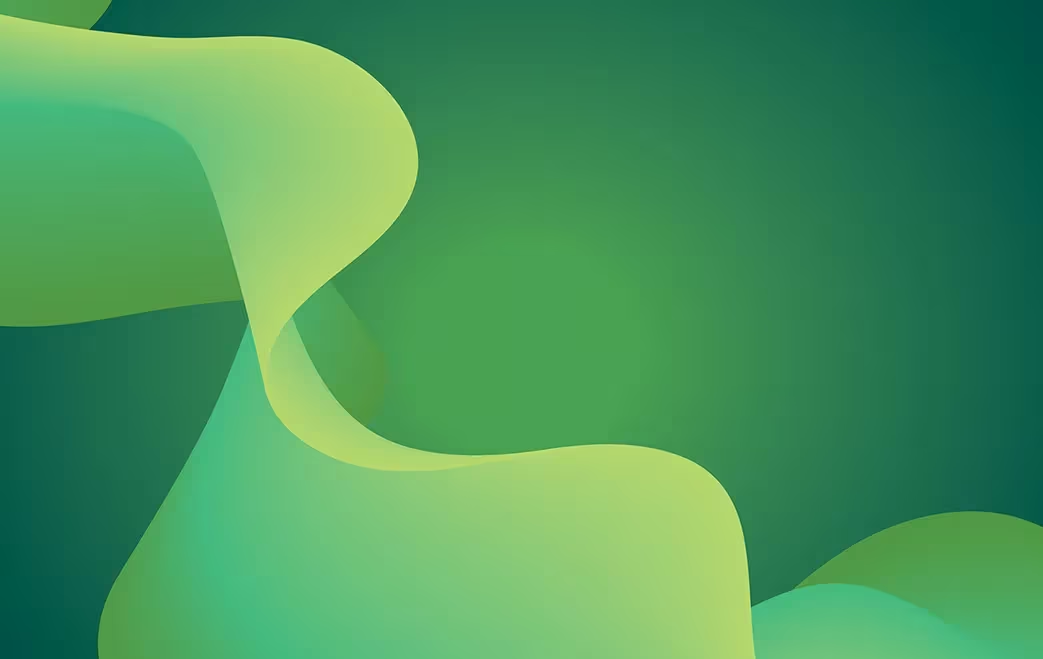
The Algae revolution.
With its algae-based materials, the Swiss start-up Noriware is pioneering sustainable packaging solutions.
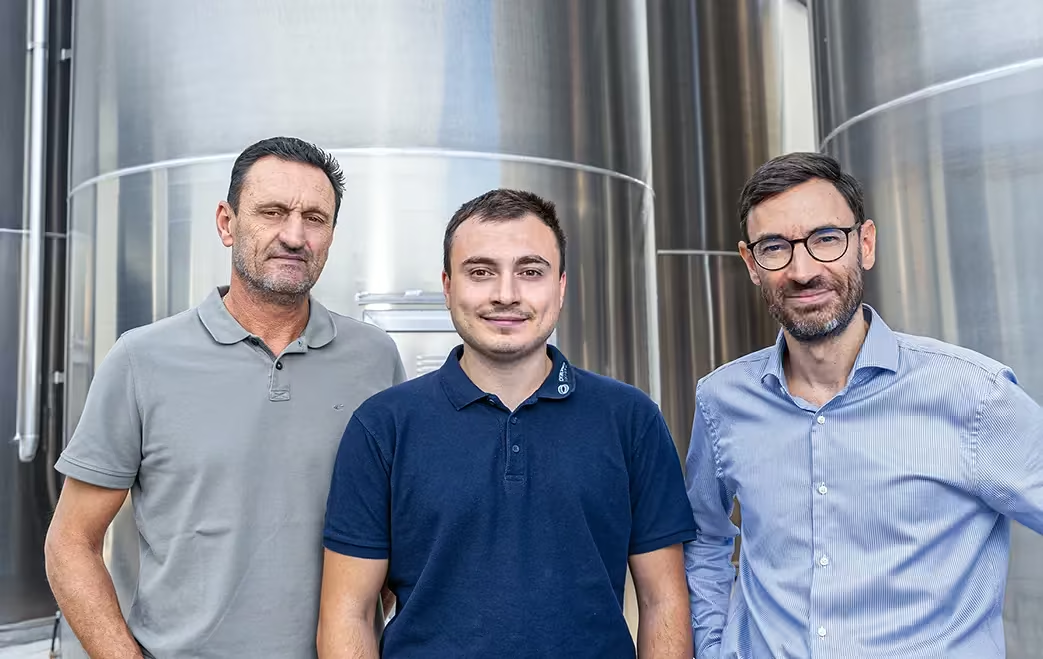
Keeping balance.
Kotronis Packaging, located near Nafpaktos in western Greece, is one of the country’s leading producers of thin-walled packaging for the food industry.
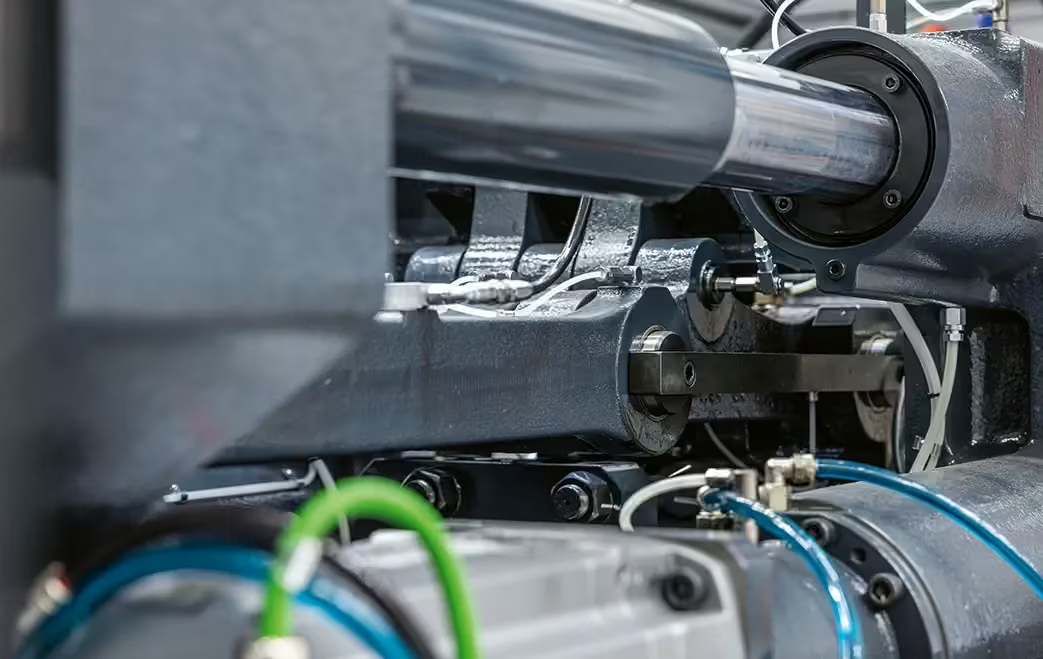
Powerduo.
Powerduo: Optimized Production Solution for Large-Volume PET Preforms by Otto Hofstetter AG & Otto Systems
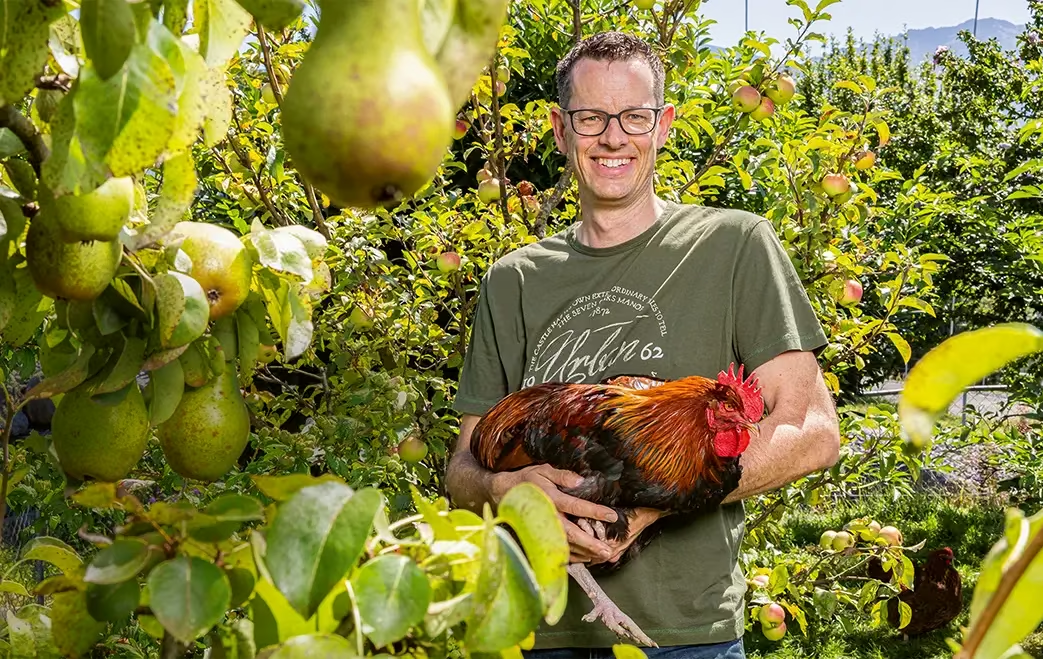
Standardsetter.
Standardsetter: Jules Müller on Leadership, Precision, and Innovation at Otto Hofstetter AG
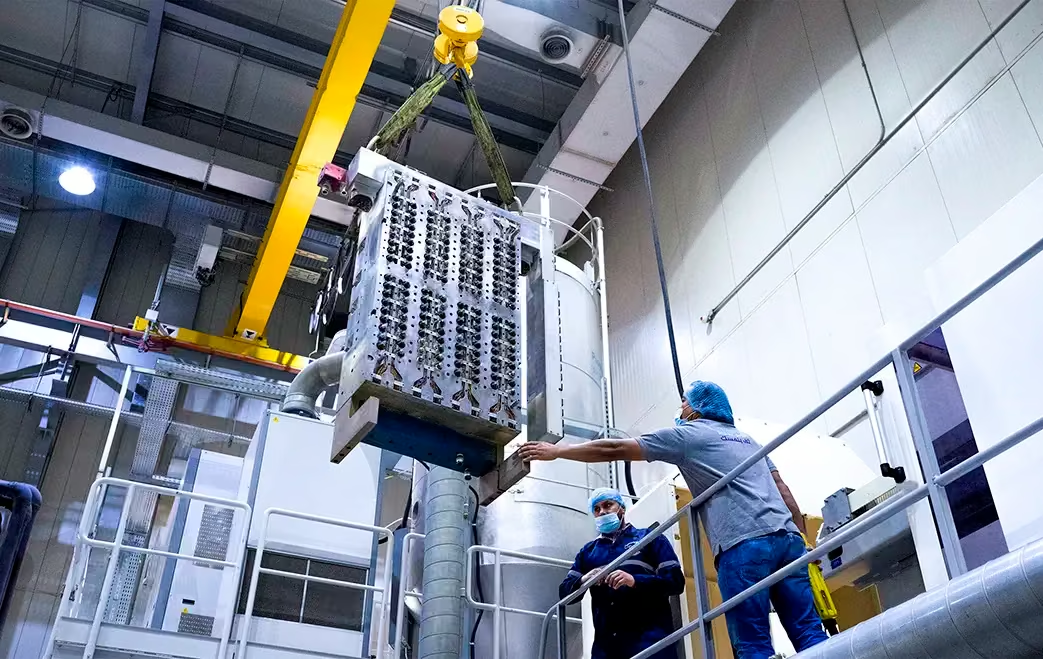
Record breaker.
Record breaker – Otto Hofstetter AG's hot-runner exchange restores production in just two days.
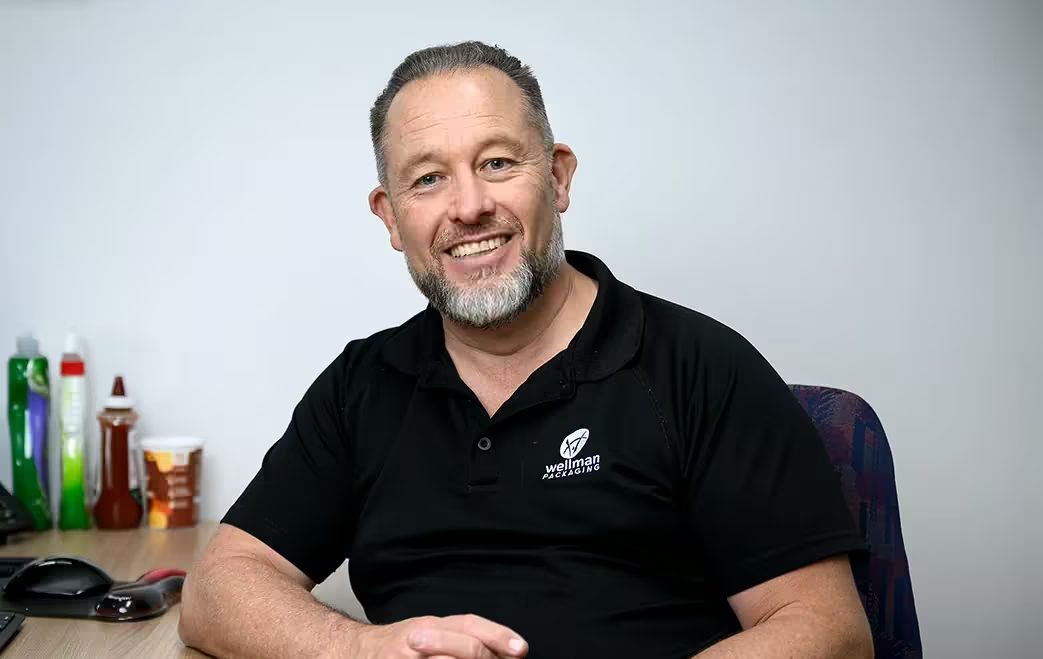
Positive Impact.
Positive Impact: Craig Wellman on Innovation, Sustainability, and the Future of Plastic Packaging at Wellman Packaging
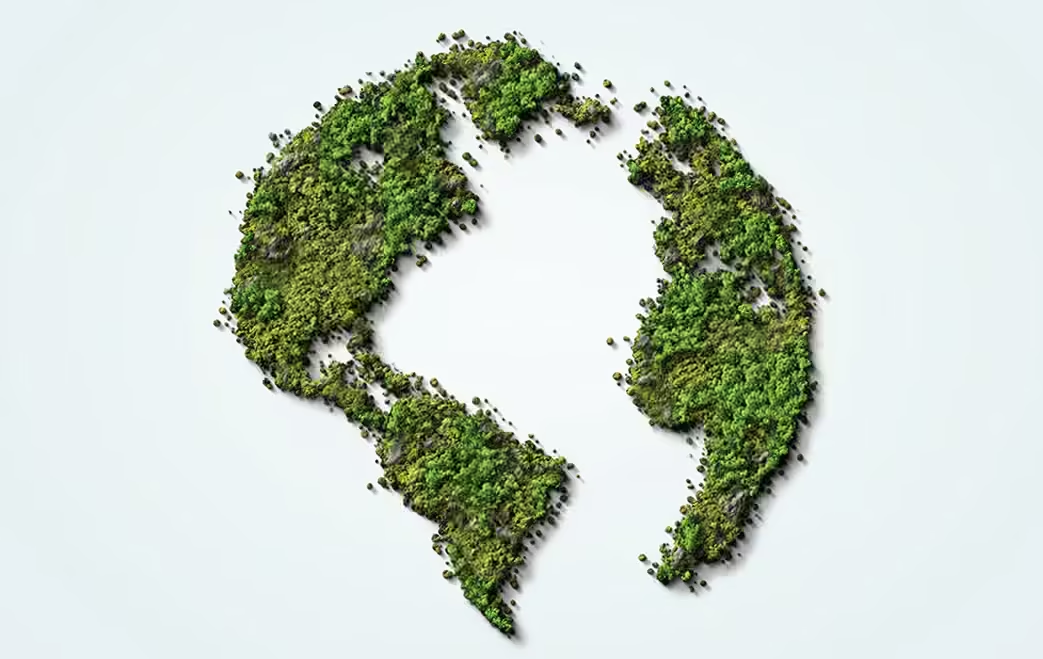
Sustainability confirmed.
Otto Hofstetter AG is strengthening its sustainability efforts, aligning with global ESG standards and preparing for GRI-compliant reporting by 2025. Learn how the company is driving transparency and responsibility for a greener future.
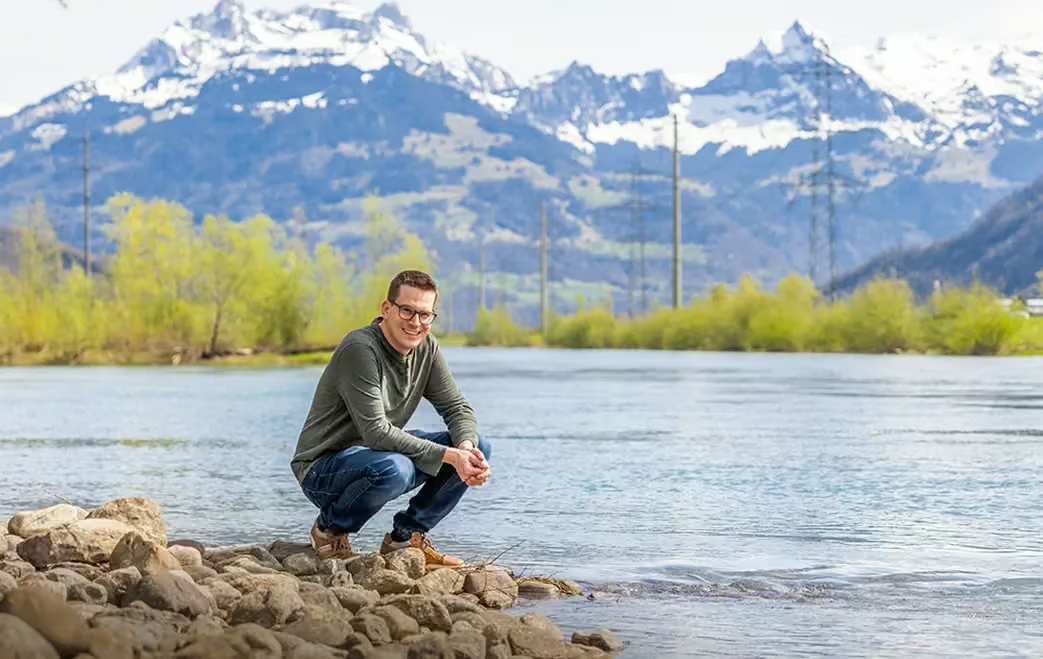
Just no routine.
For twenty years, Philipp Hofstetter has embraced new challenges at Otto Hofstetter AG, growing from an apprentice to head of HSC milling. Passionate about teamwork and digitalization, he sees great potential for the future while staying true to his hands-on approach.
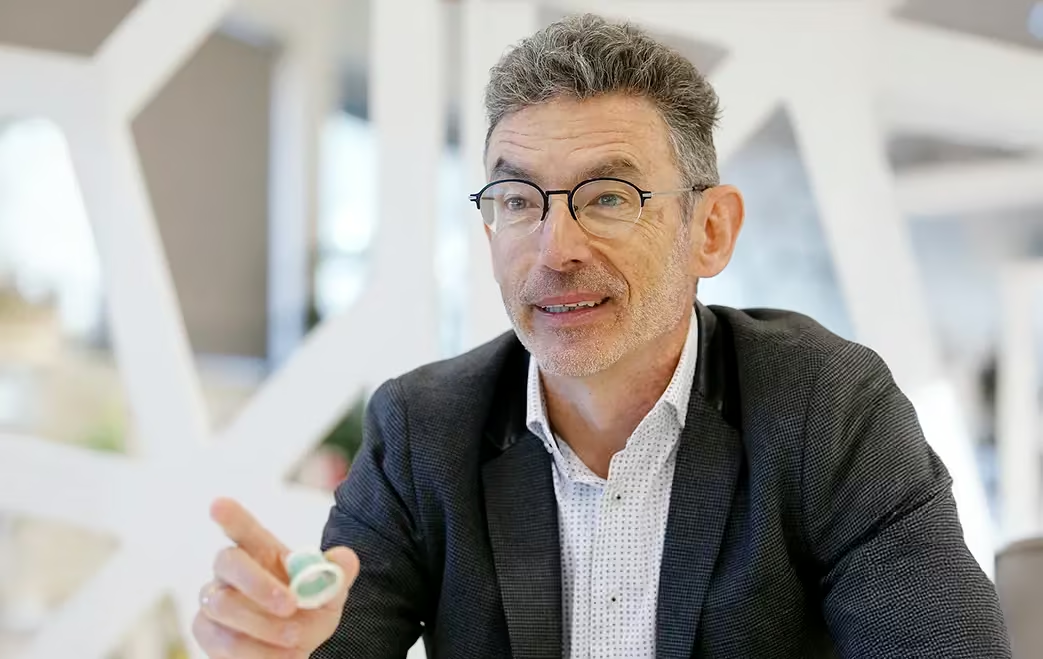
Never stop.
Never stop – Capsul’in Pro’s journey of innovation in coffee capsule technology
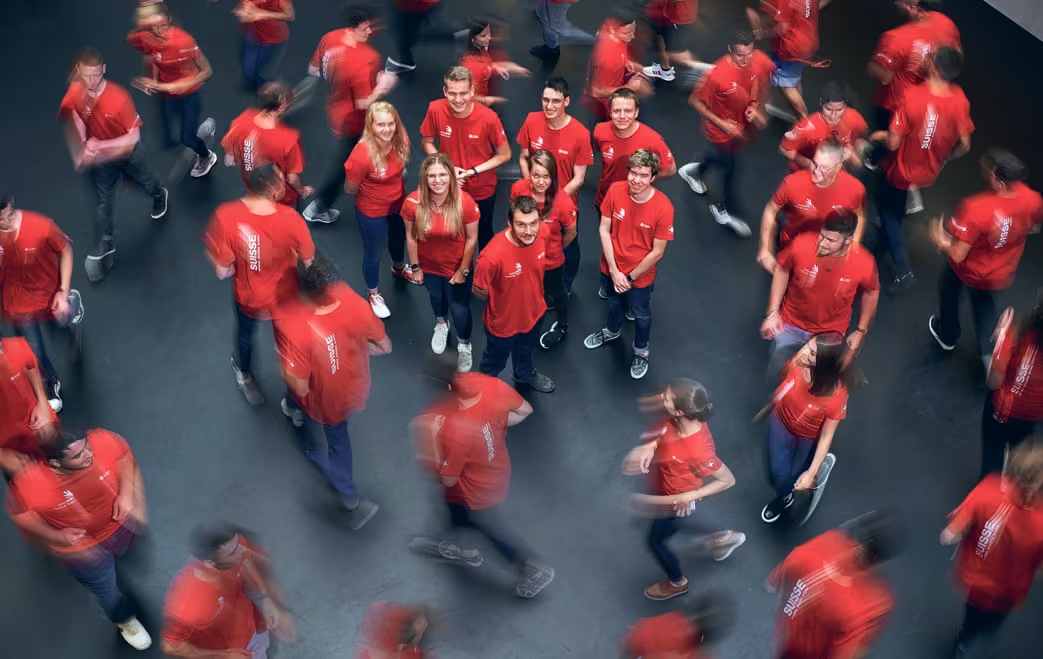
The origins of Swiss quality.
Swiss quality is world-renowned, built on a centuries-old tradition of innovation and precision. At the heart of this excellence is the country’s unique dual vocational training system. Discover how this approach shapes industries and ensures future success, with Otto Hofstetter AG playing its part in training the next generation of experts.
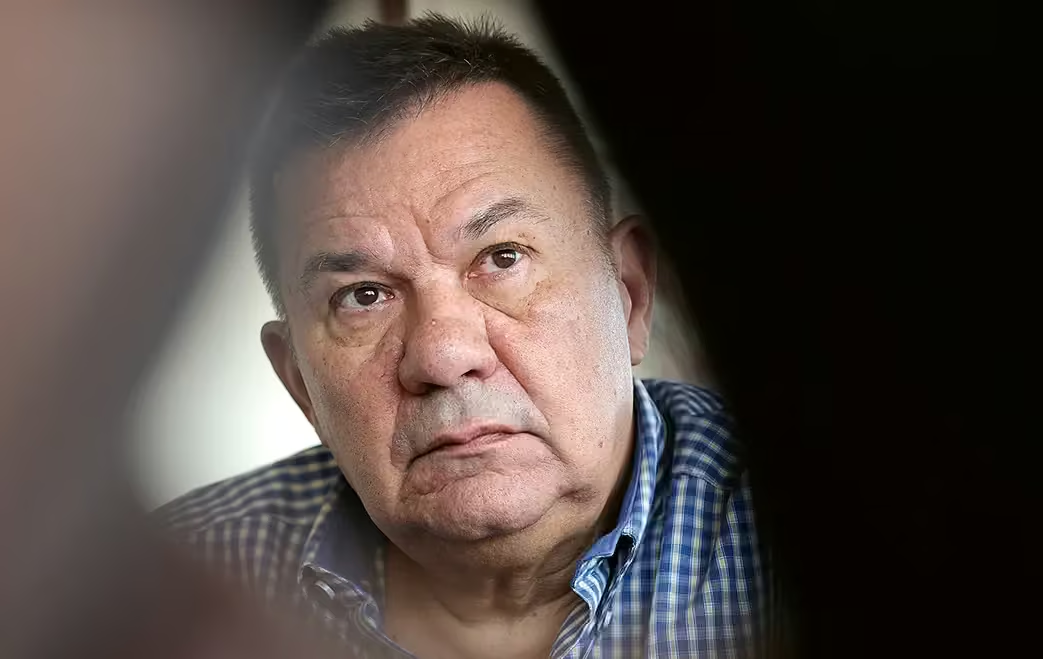
Always available.
EnergoPET, a leading PET preform producer in Serbia, operates 24/7 to manufacture 1.2 billion preforms annually. Managing Director Miroslav Popović discusses the company’s history, growth strategy, and commitment to innovation, quality, and sustainability.
Ready to write your success story with us?
Contact us today to explore how our expertise in high-precision moulds for PET preforms, packaging solutions, and medical applications can help drive your success.