The exceptional reliability and durability of Otto Hofstetter AG's moulds are well known in the industry. Mould availability of over 98 percent and up to 20 million cycles before the first maintenance are benchmarks that speak for themselves. The low wear of moving parts in our moulds and the wide range of maintenance and overhaul options guarantee exceptional longevity. What’s more, conversions and adjustments can be easily implemented, as the main components of the moulds are designed for extreme durability. Clearly, this kind of mould performance can only be achieved through the careful selection of the materials used to make them.
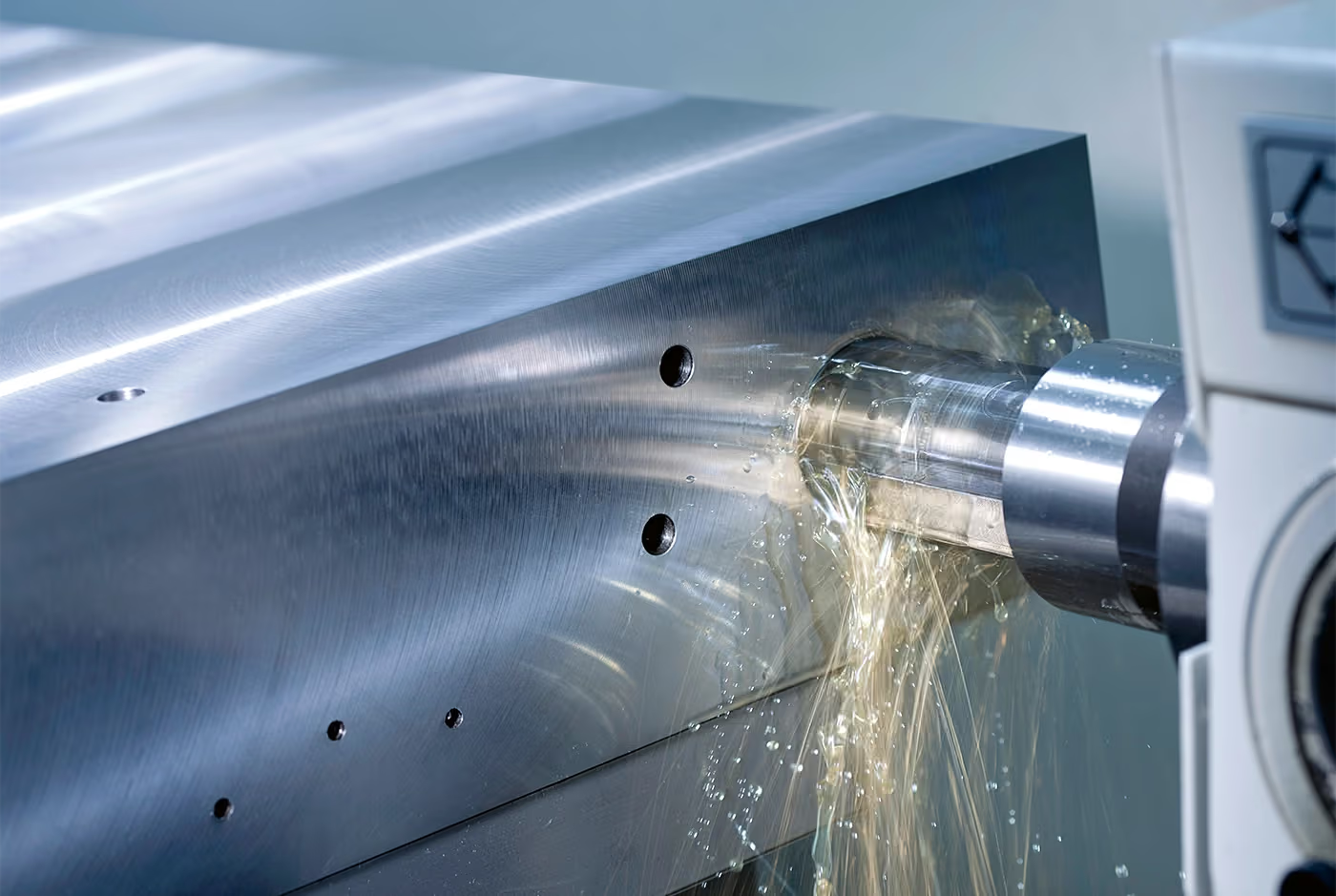
Tailor-made materials
Otto Hofstetter AG's moulds are used around the world and they have to function under a wide range of climatic conditions – from regions with high humidity to arid deserts. In all cases, they must withstand the stresses caused by plastics that are processed at temperatures as high as 300° C. Thus, the steel we use must be of the highest quality. The basic structure of our moulds is made of a distortion-free and corrosion-resistant plastic mould steel called THYROPLAST-2294, which also has the advantage of being particularly easy to machine.
The actual moulding parts of the mould are made of THYROPLAST-2083 ESU. This steel is produced using the electro-slag remelting process, which significantly improves its purity. After soft machining, it is hardened to 50-52 HRC, which makes the steel optimally corrosion-resistant and easy to polish.
Quality through partnership
The collaboration with thyssenkrupp Materials Schweiz AG is based on mutual trust and the joint pursuit of optimal solutions. Through our detailed process understanding, the material specifications can be continuously improved. Otto Hofstetter AG shares its comprehensive process know-how with thyssenkrupp Materials Schweiz AG, which enables a precise analysis of the relevant parameters and the ongoing optimisation of the special steels that we need.
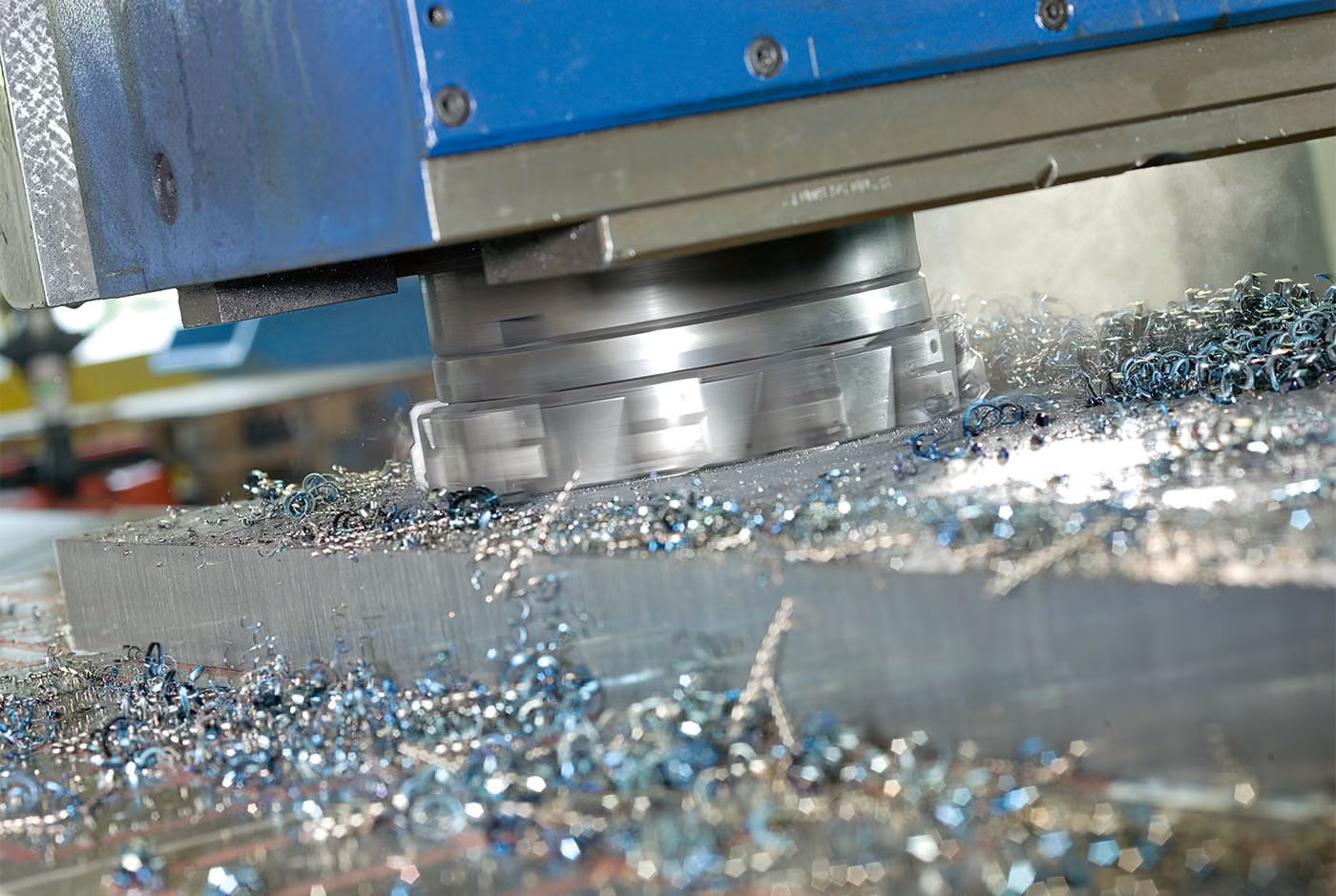
Around 80 percent of the steels used in Otto Hofstetter AG moulds comes from Germany, and 15 percent from Italy. The longstanding connection to the steelworks and the close cooperation we enjoy with their management guarantee the consistently high quality of our moulds.
Focus on sustainability
The topics of sustainability are increasingly important in the development and production of injection moulds. The THYROPLAST-2294 steel that is currently used already consists of 61 percent scrap, which significantly reduces its ecological footprint. The steel’s CO2 footprint mainly depends on how it is produced and the additives required. In essence, a higher scrap content reduces the environmental footprint.
The materials in Otto Hofstetter AG's moulds are of such high quality that even after their service life has come to an end, our moulds can be collected, processed and recycled back into production. The valuable alloy components, such as chromium, are an important resource in corrosion-resistant mould steels.
Otto Hofstetter AG has launched several projects to further improve mould performance and reduce the environmental impact of its steels, which is already internationally competitive. We will regularly our update progress in this area in future issues of InForm.
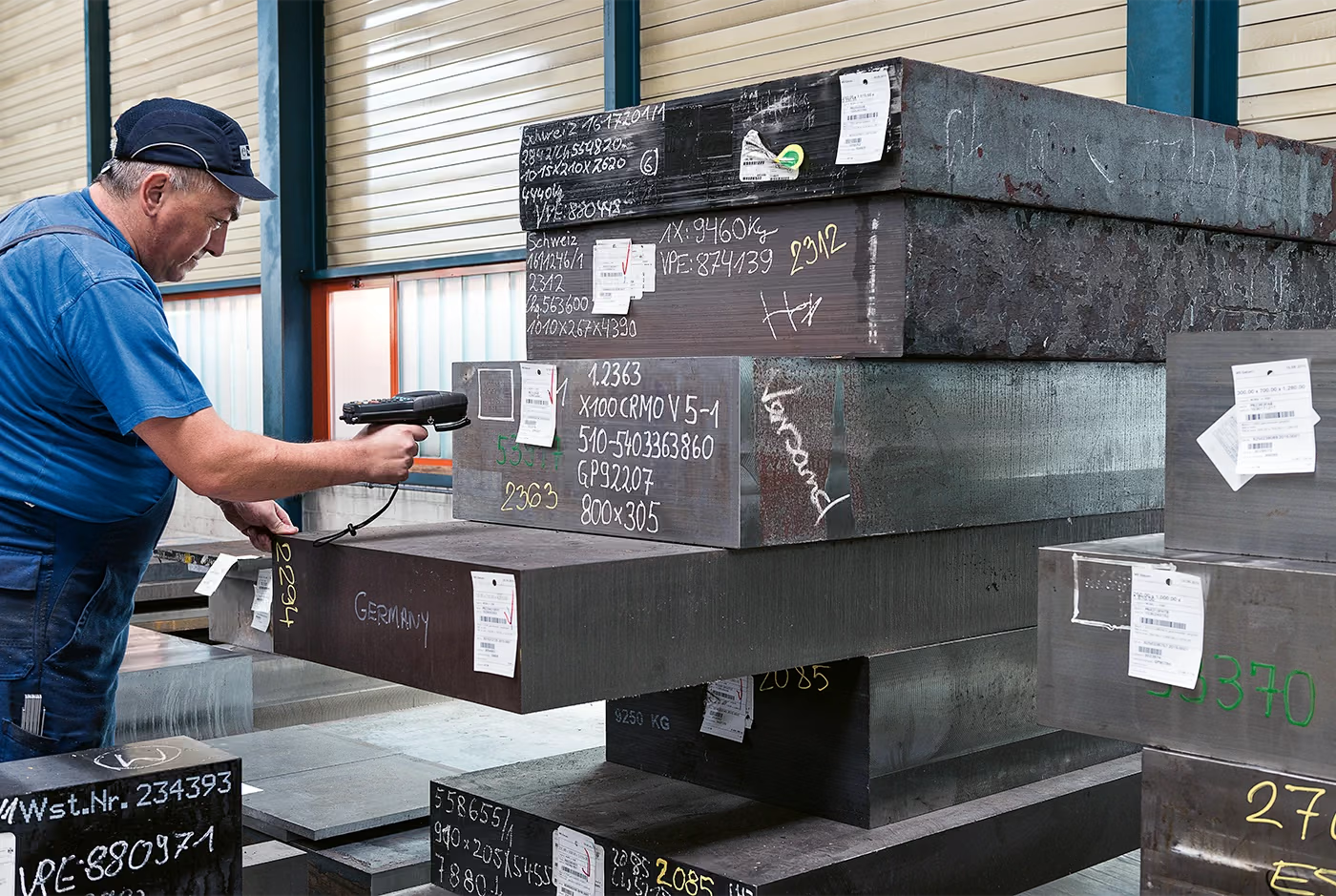