Downloads
Industry expertise to drive success.
Access our library of technical documents, white papers and case studies to learn about the latest developments in mould technology and best manufacturing practices.
View all download material from Otto Hofstetter AG
Technical documents
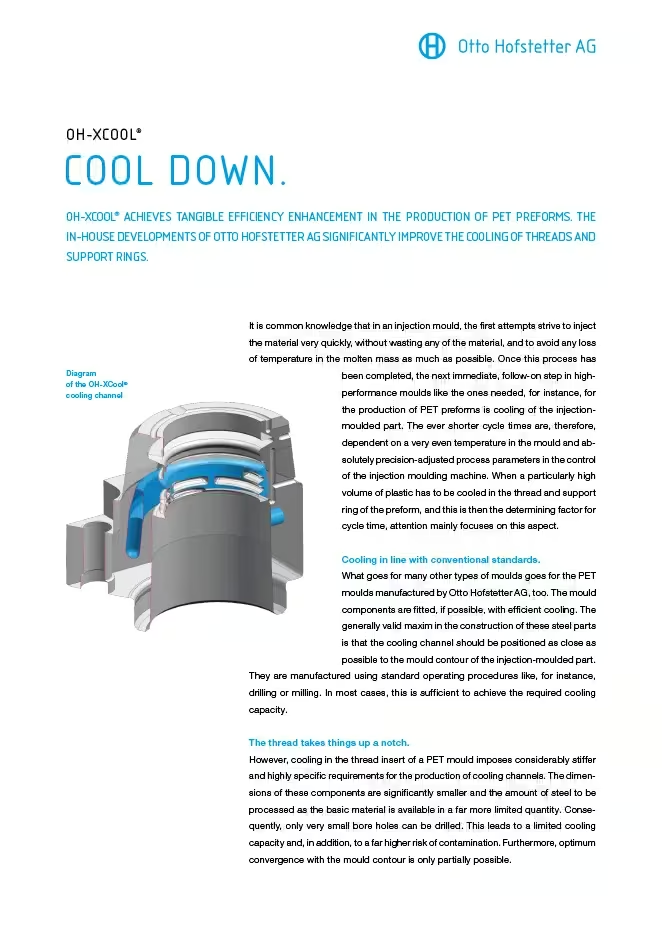
OH-Xcool factsheet
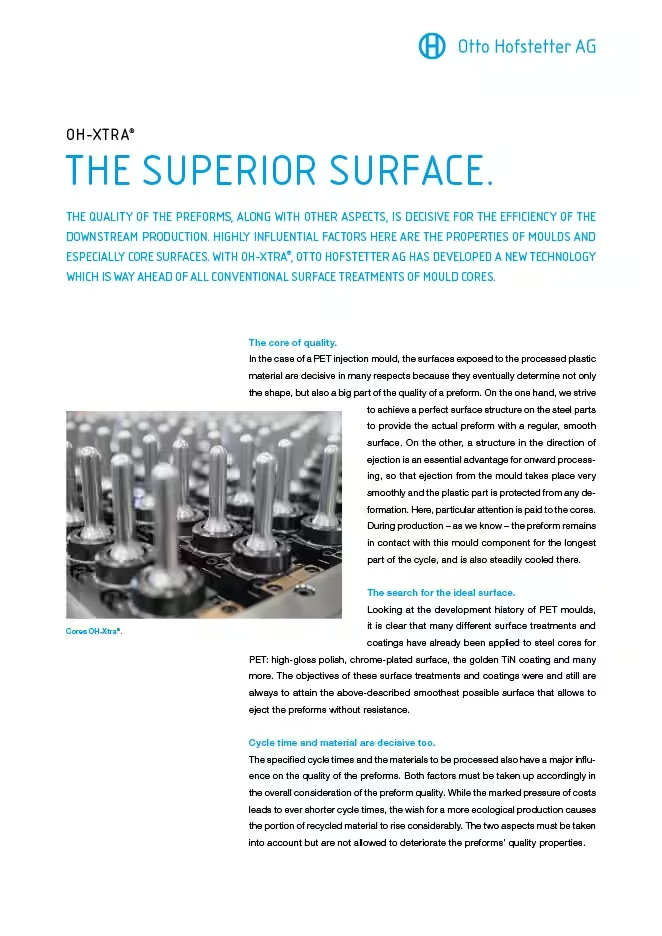
OH-Xtra factsheet
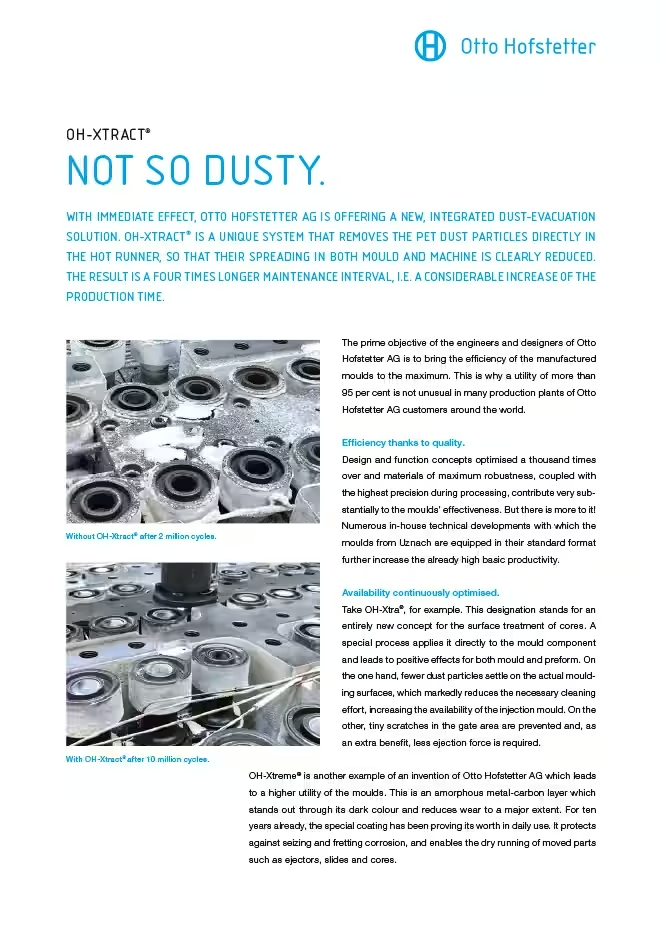
OH-Xtract factsheet
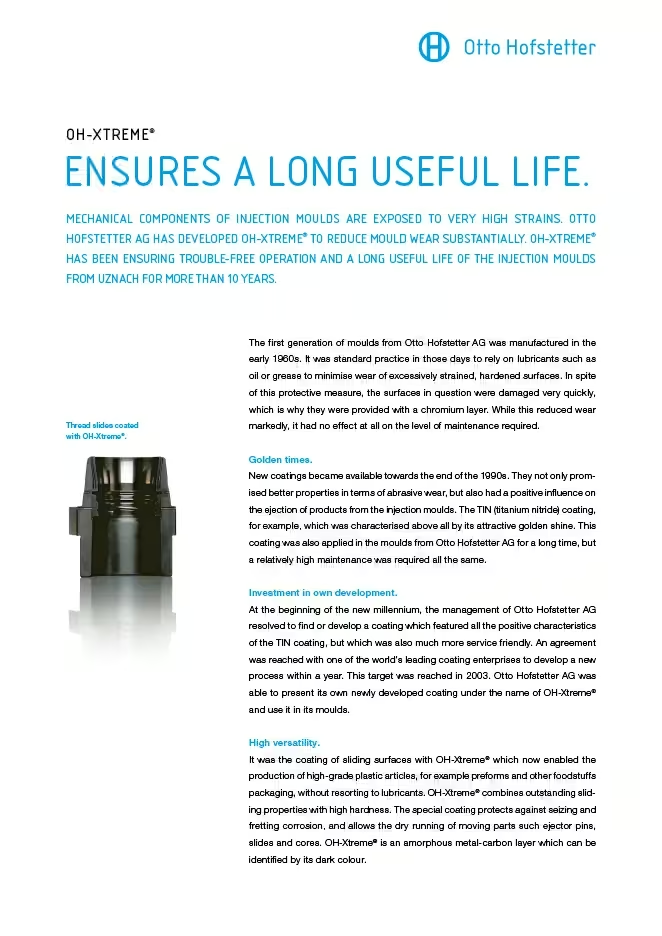
OH-Xtreme factsheet
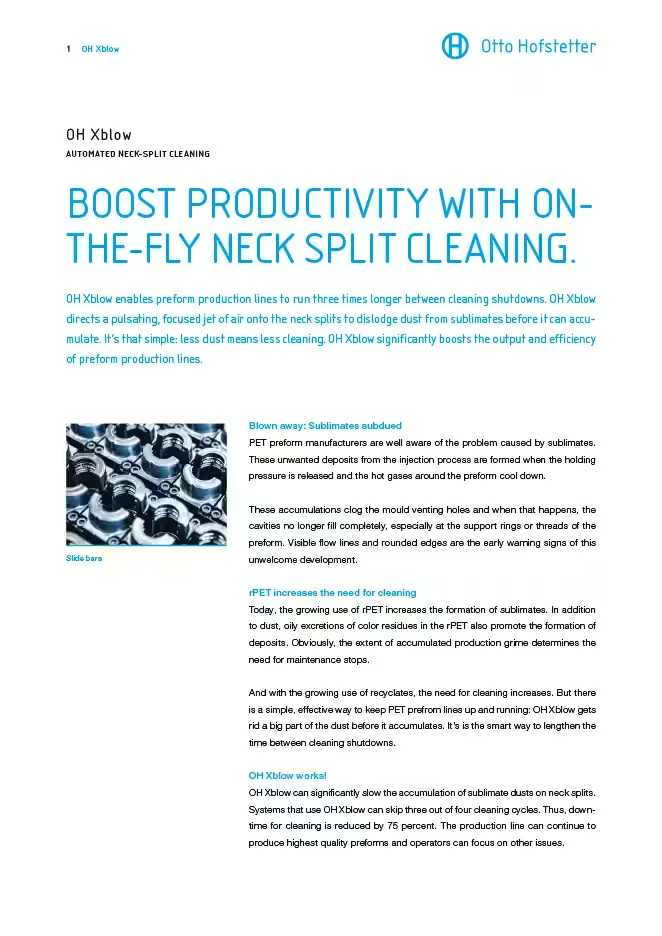
OH-Xblow factsheet
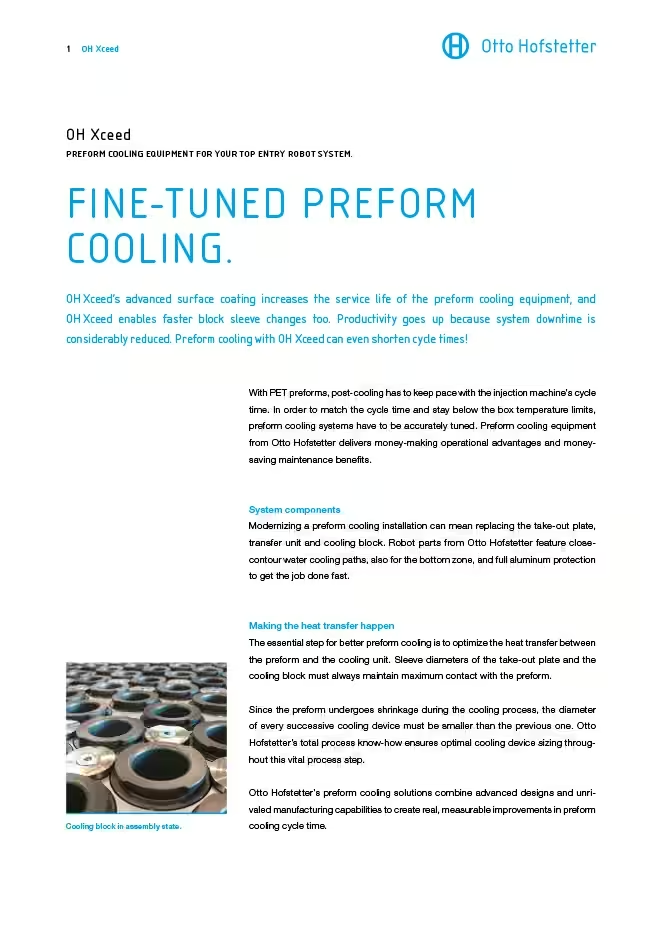
OH-Xceed factsheet
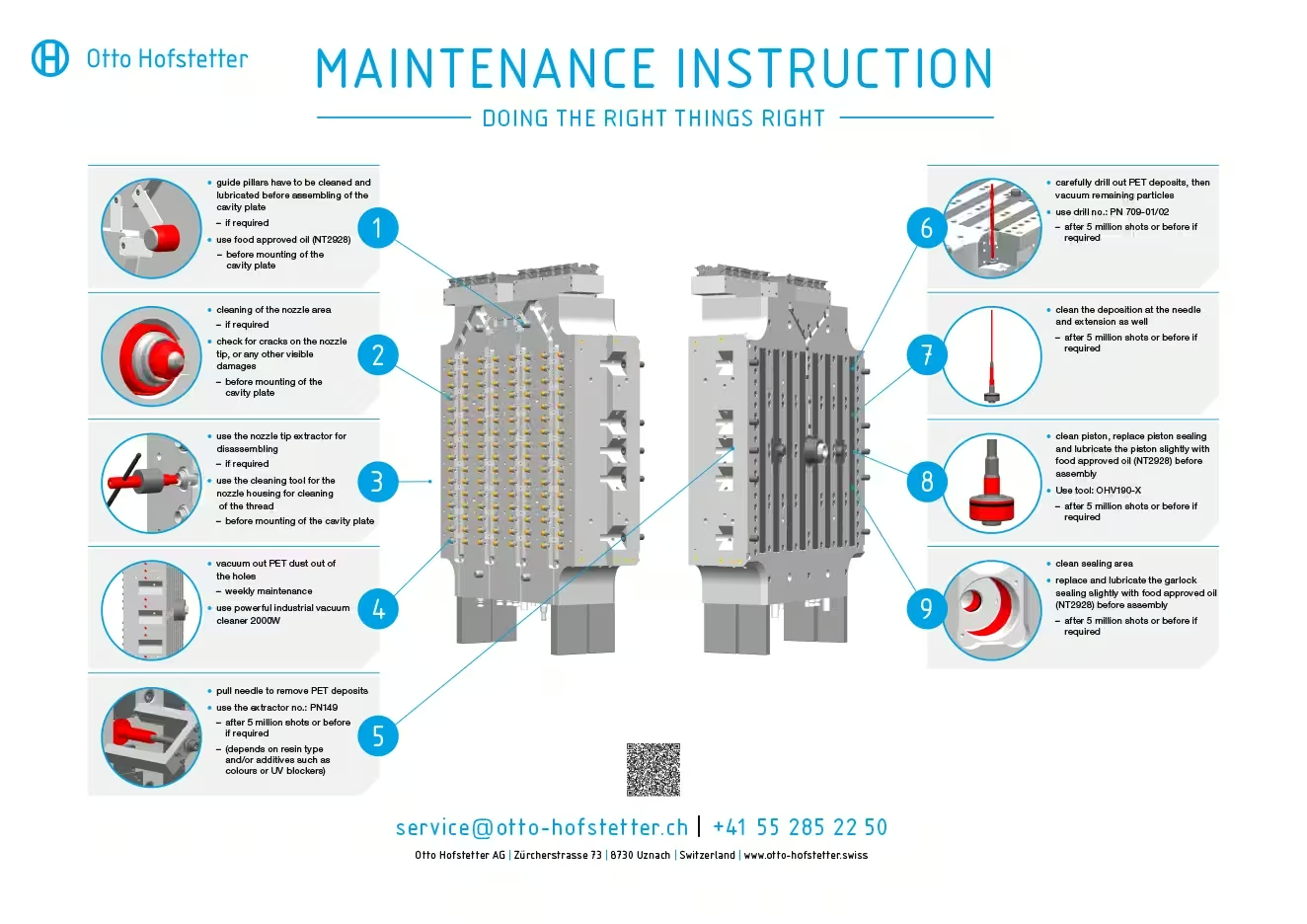
Mould maintenance instruction
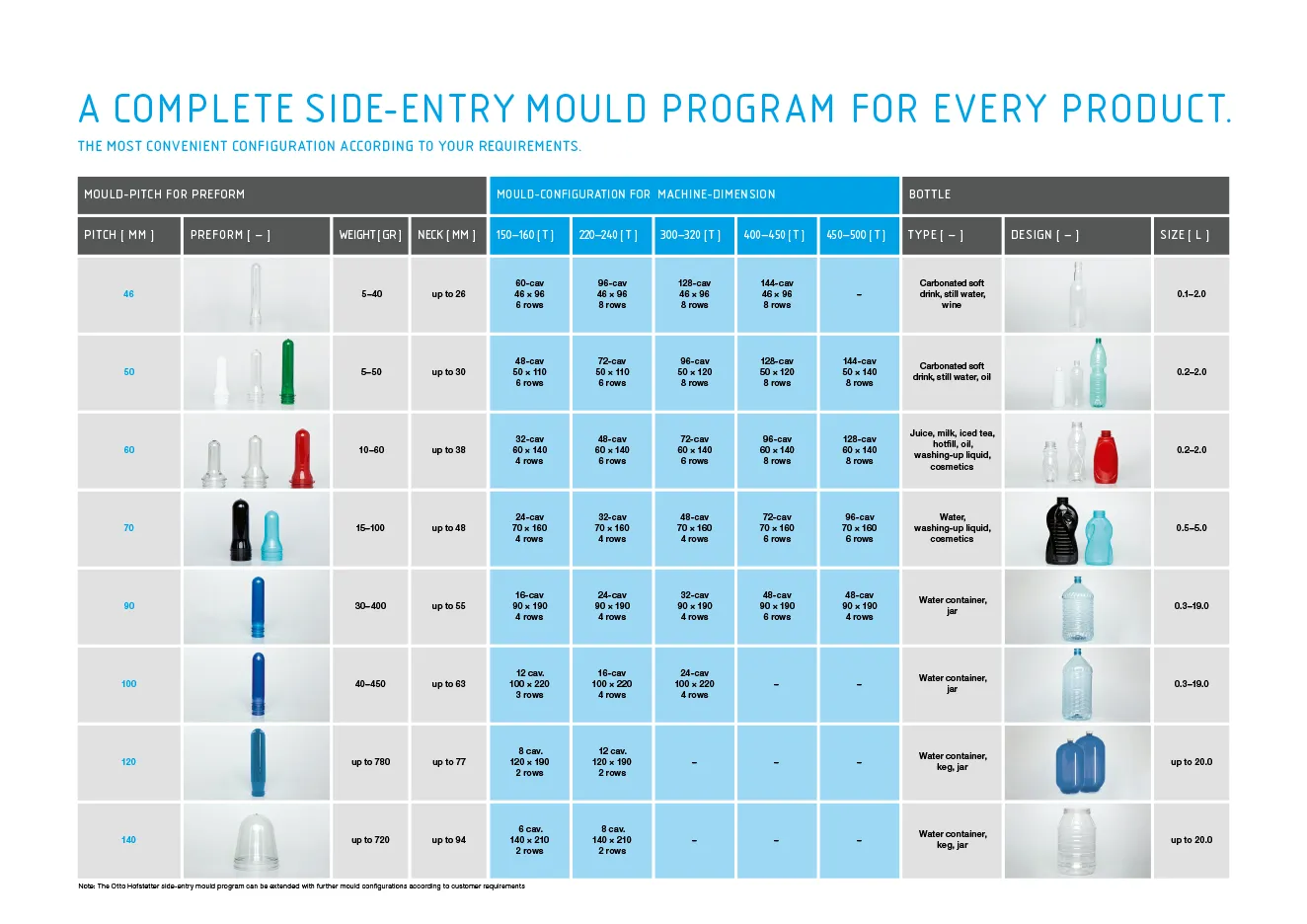
Mould Portfolio PET
Customer magazines
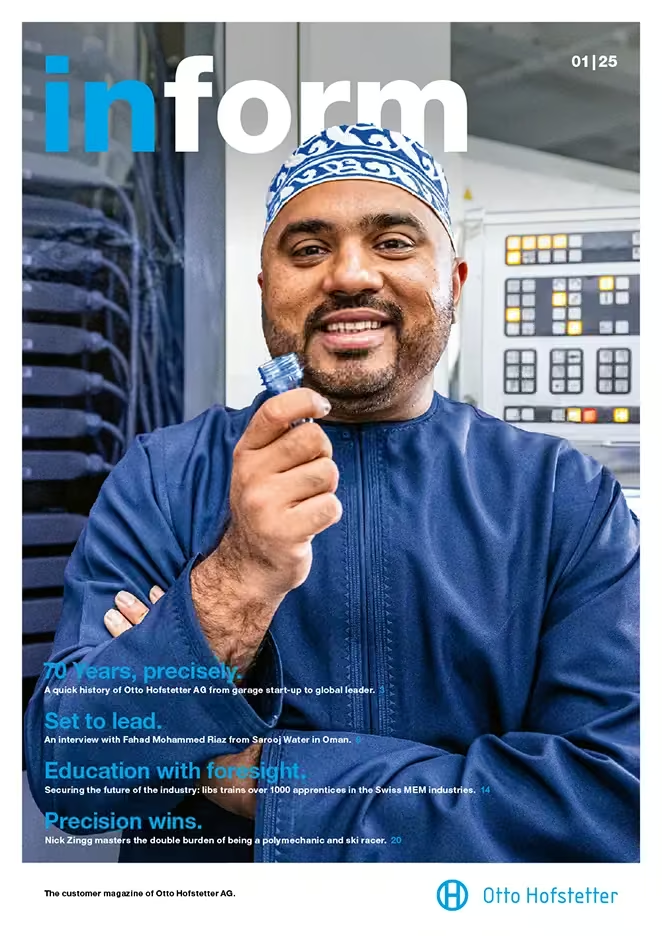
Issue 2025-1
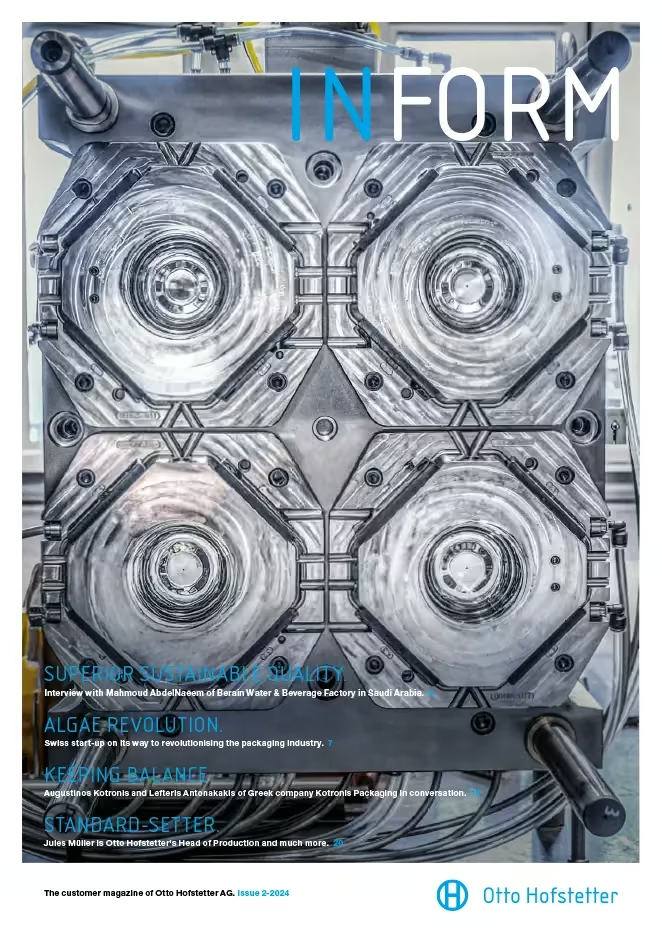
Issue 2024-2
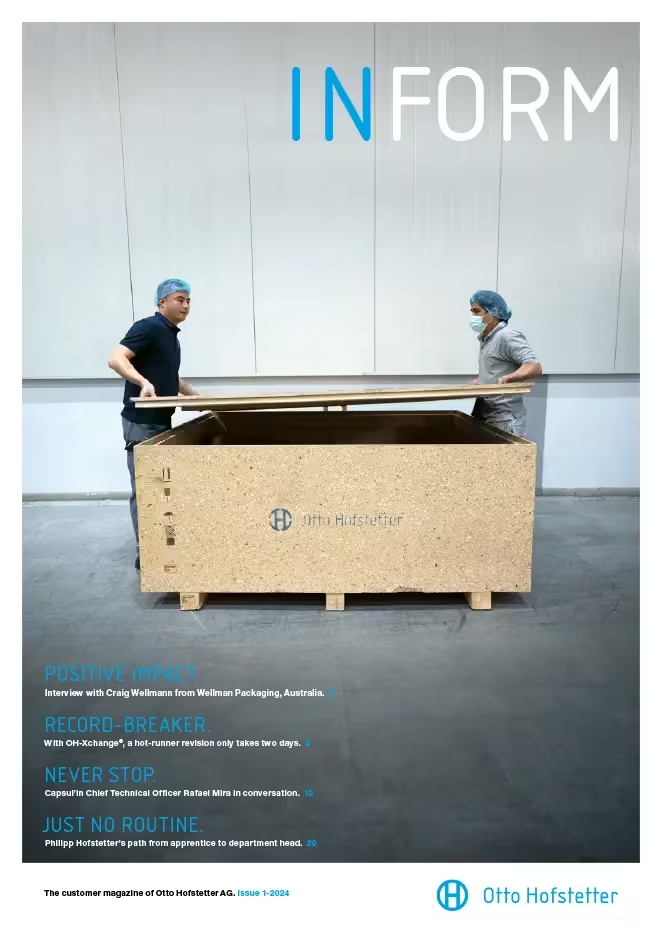
Issue 2024-1
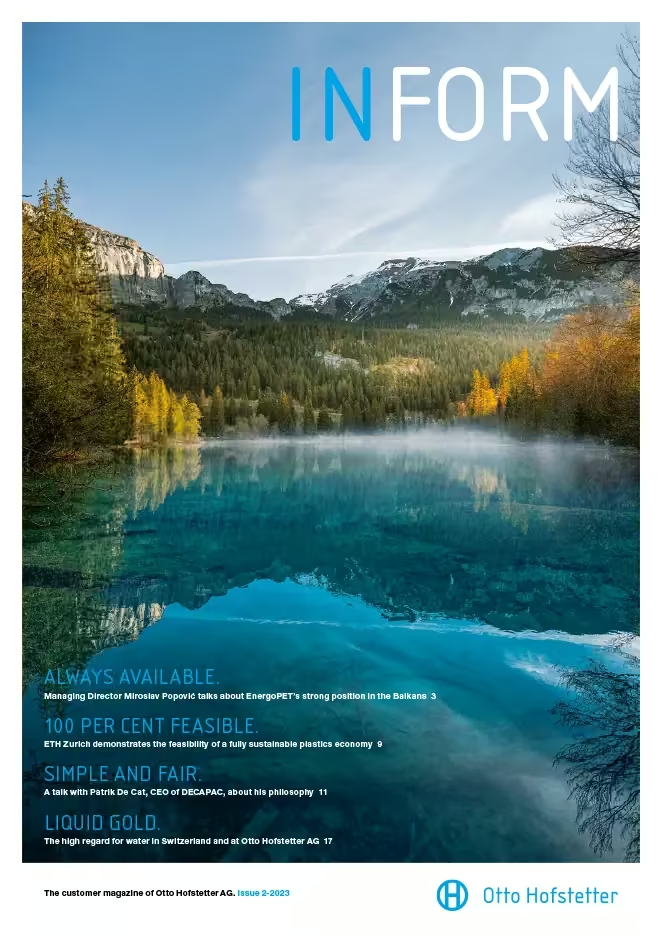
Issue 2023-2
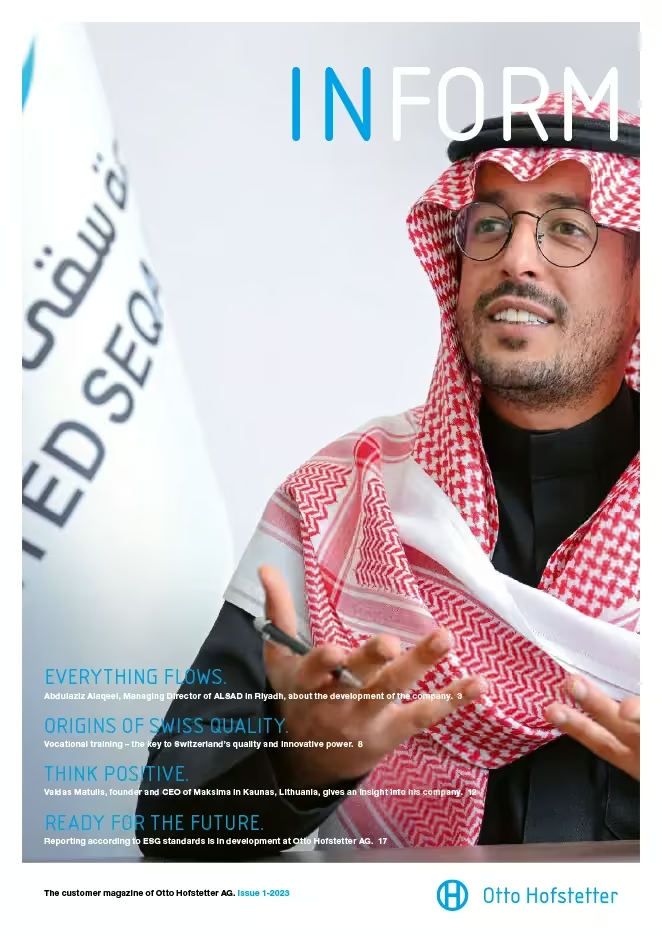
Issue 2023-1
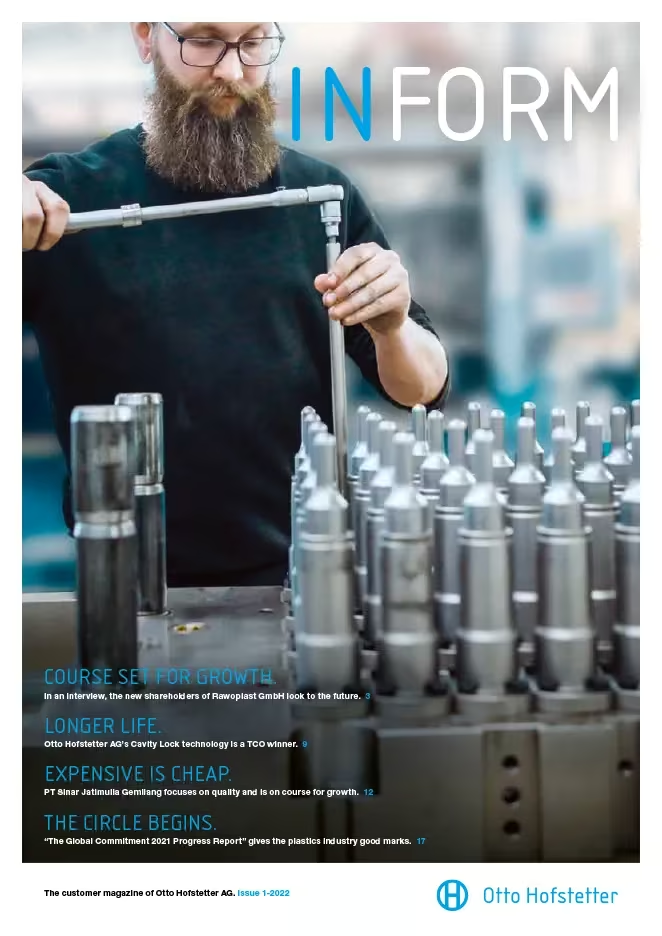
Issue 2022
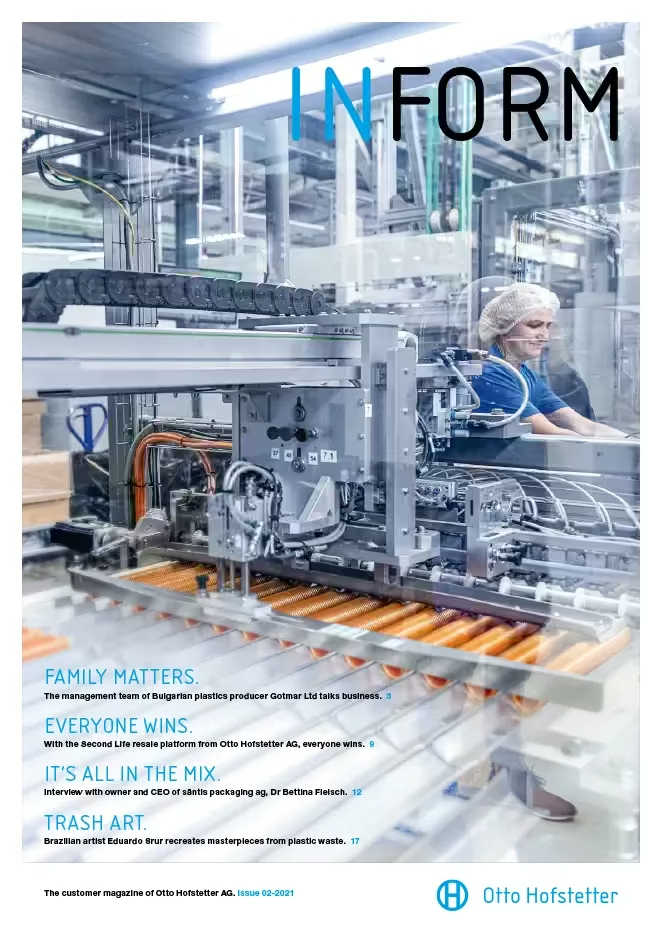
Issue 2021-2
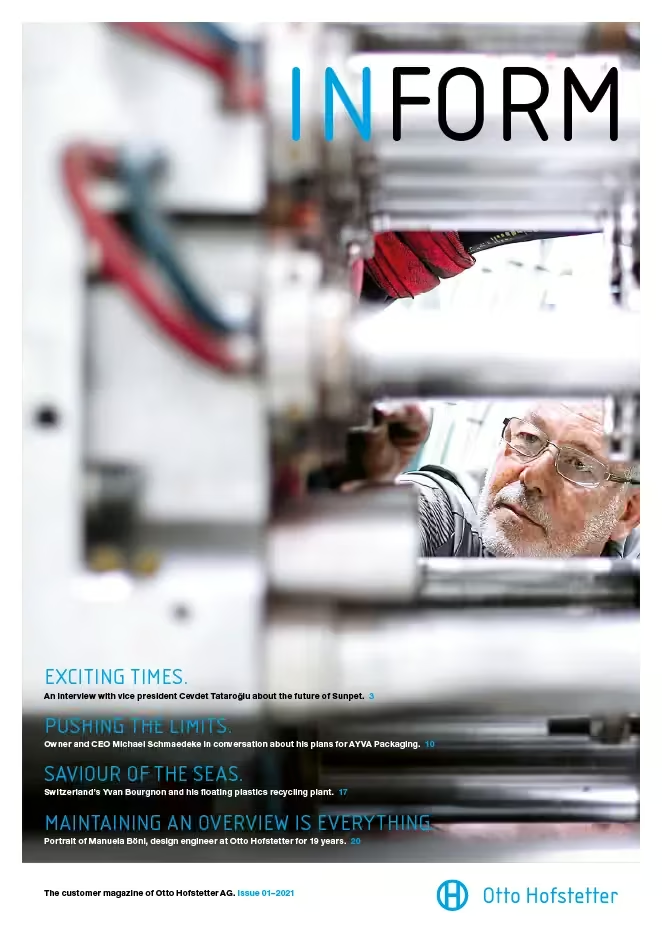
Issue 2021-1
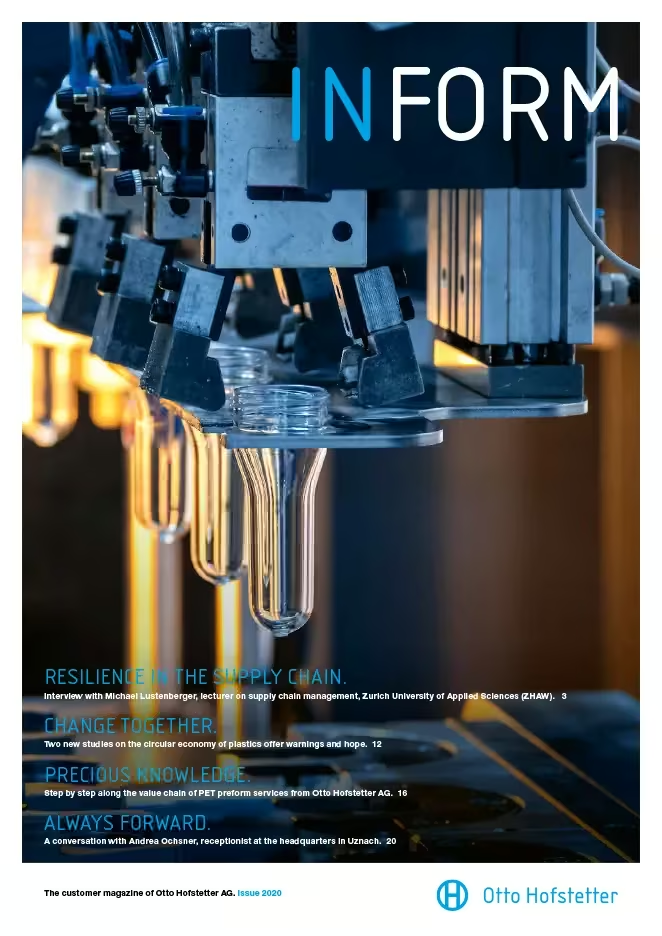
Issue 2020
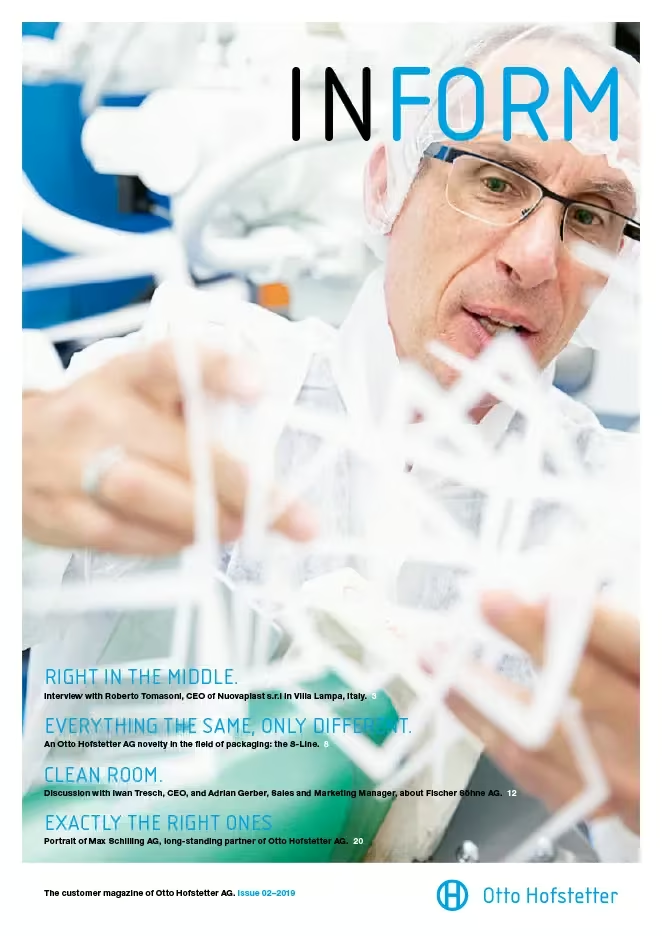
Issue 2019-2
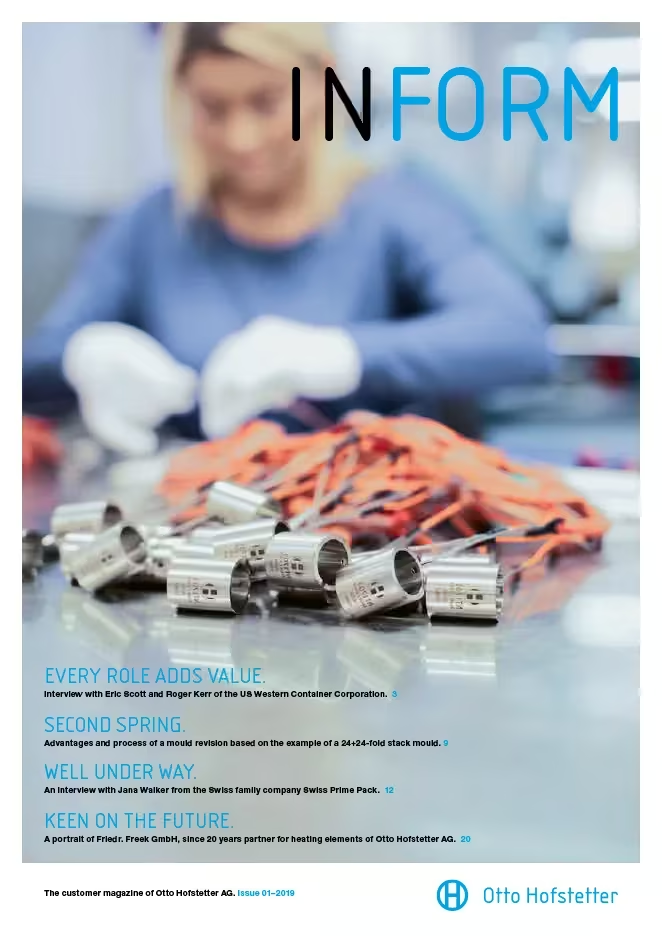
Issue 2019-1
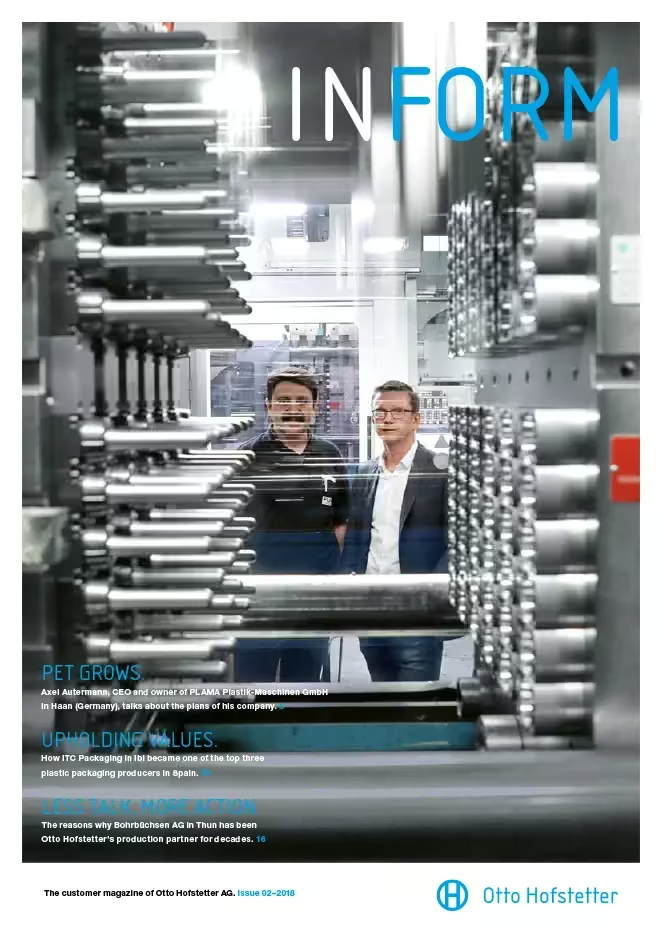
Issue 2018-2
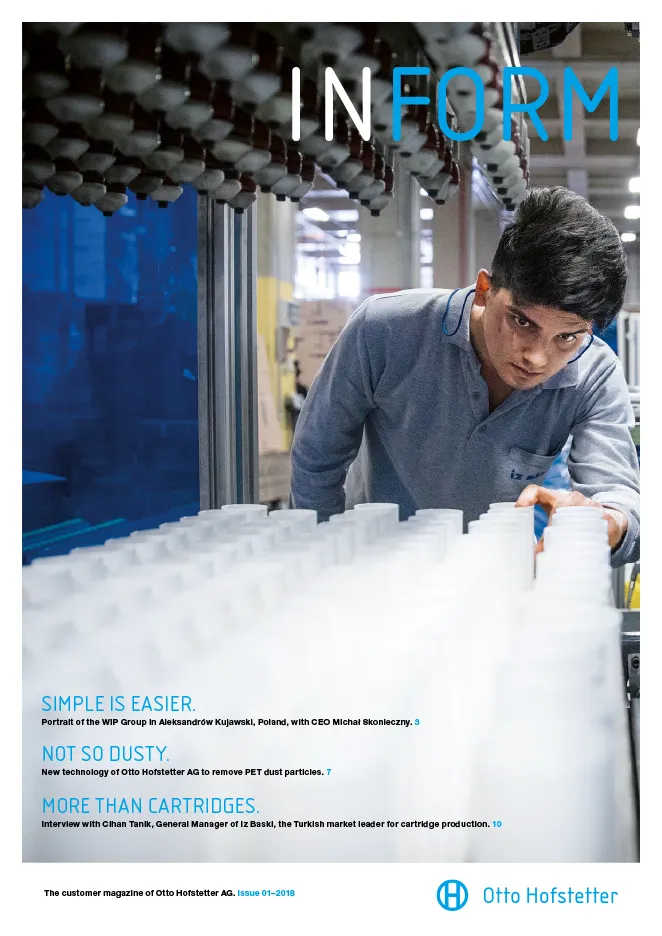
Issue 2018-1
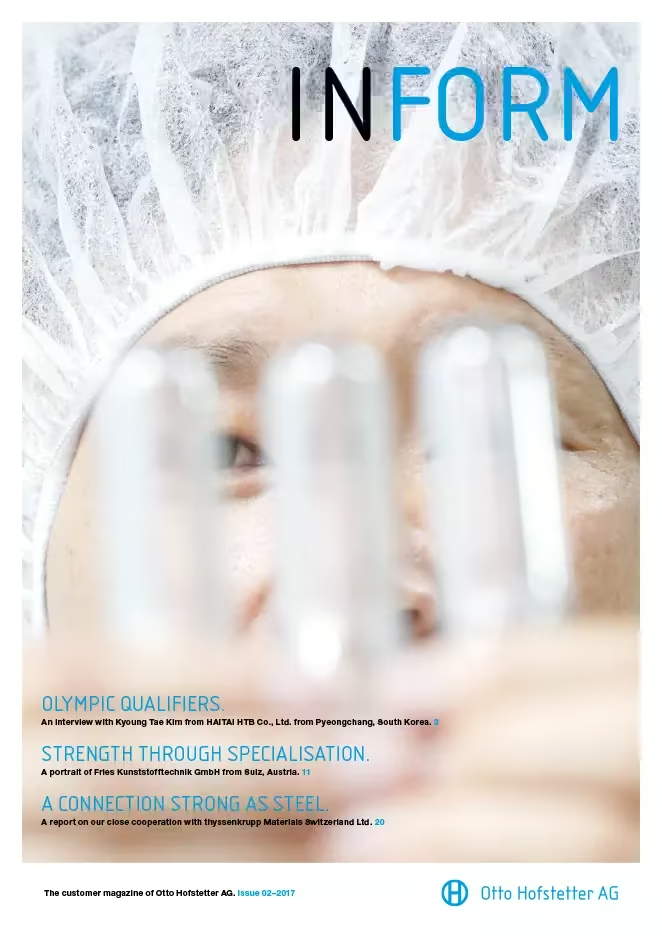
Issue 2017-2
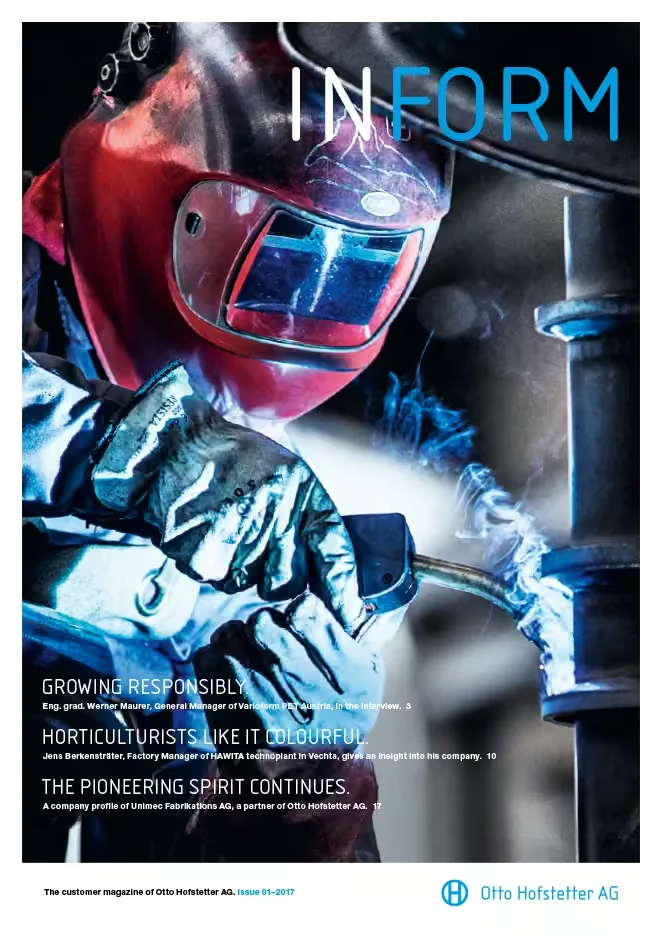
Issue 2017-1
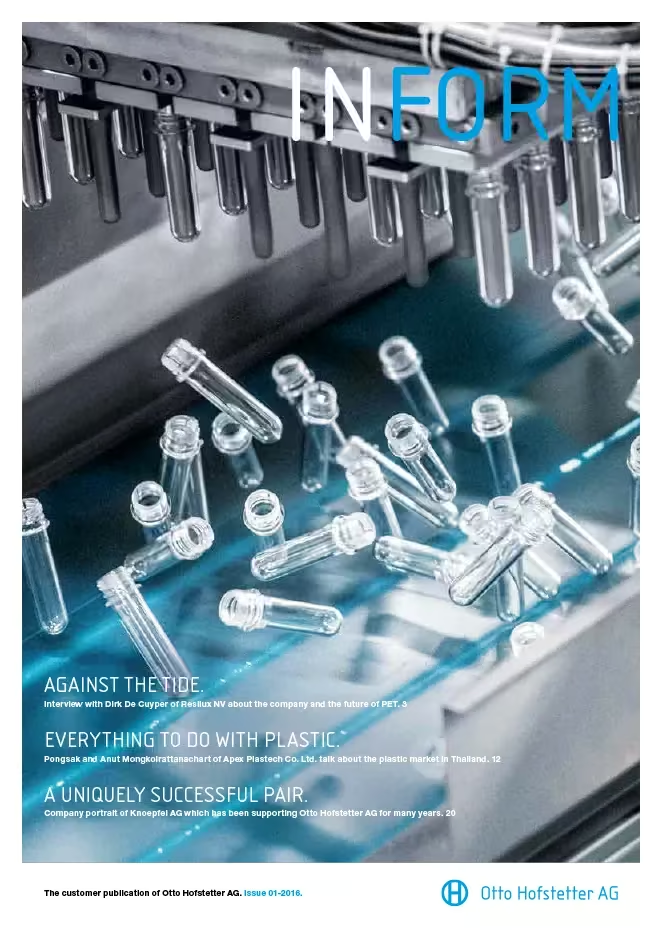
Issue 2016-1
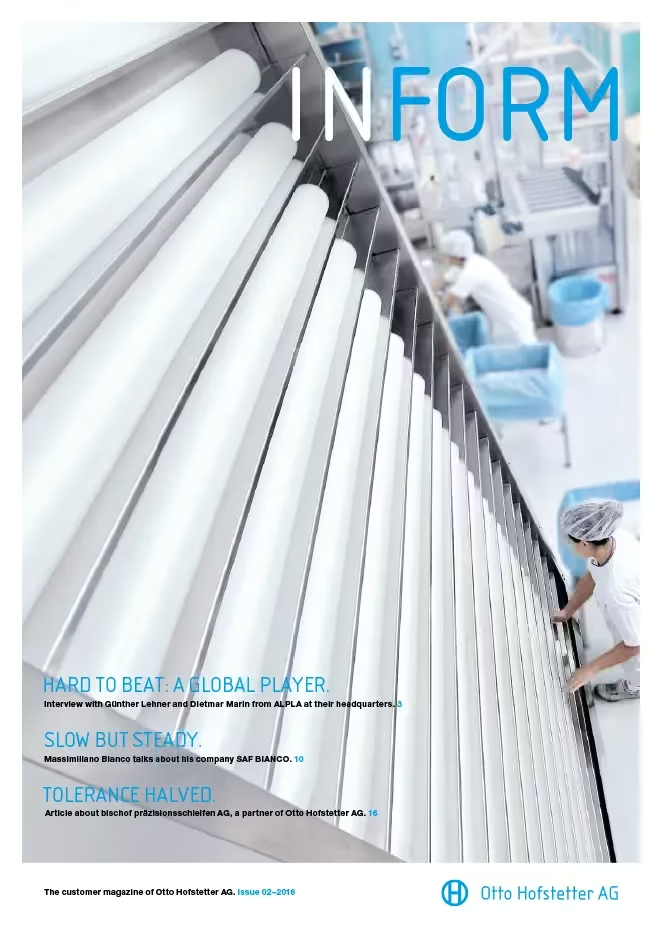
Issue 2016-2
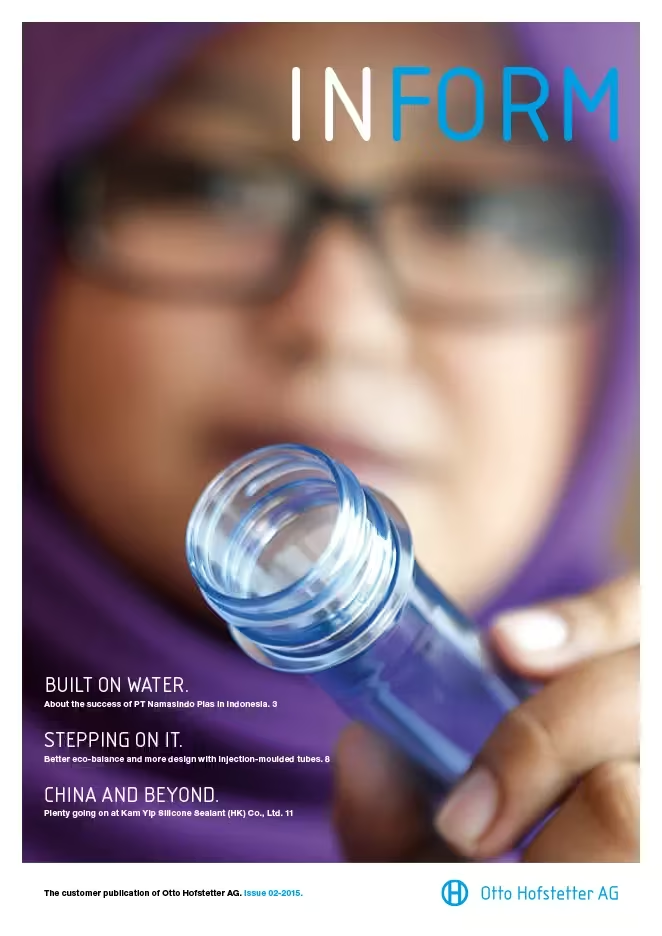
Issue 2015-2
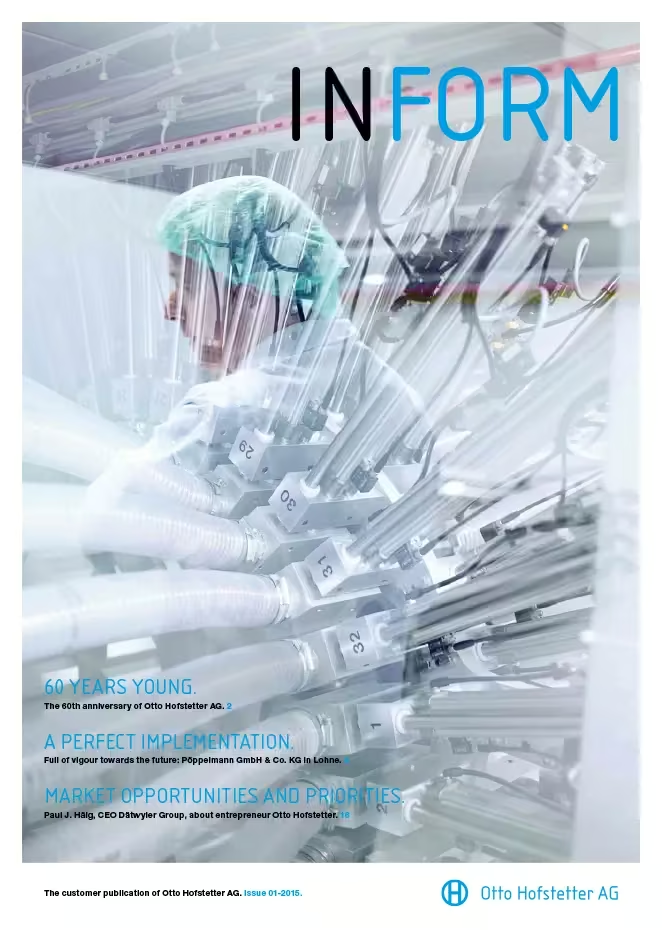
Issue 2015-1
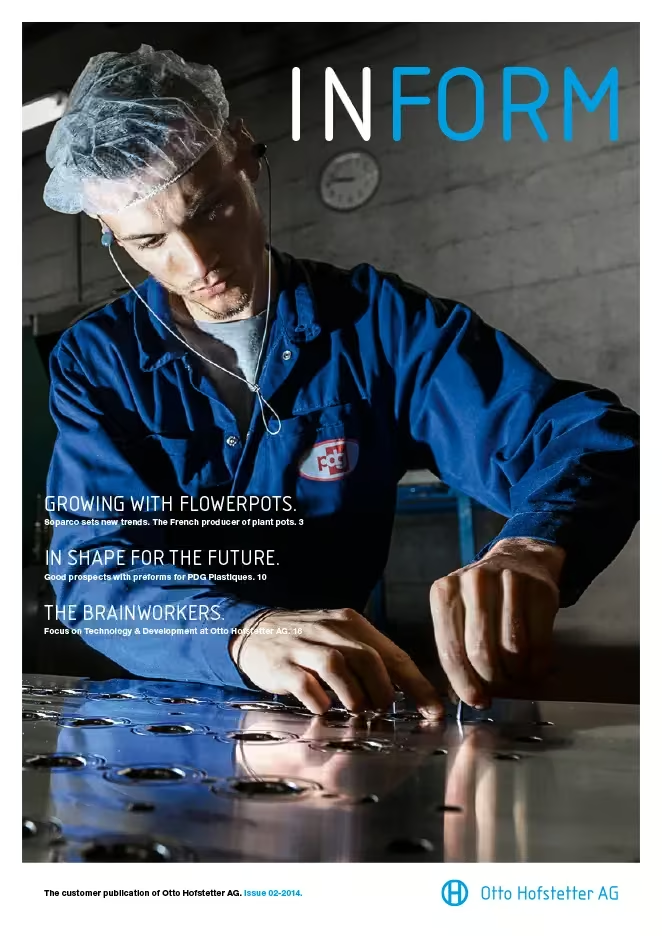
Issue 2014-2
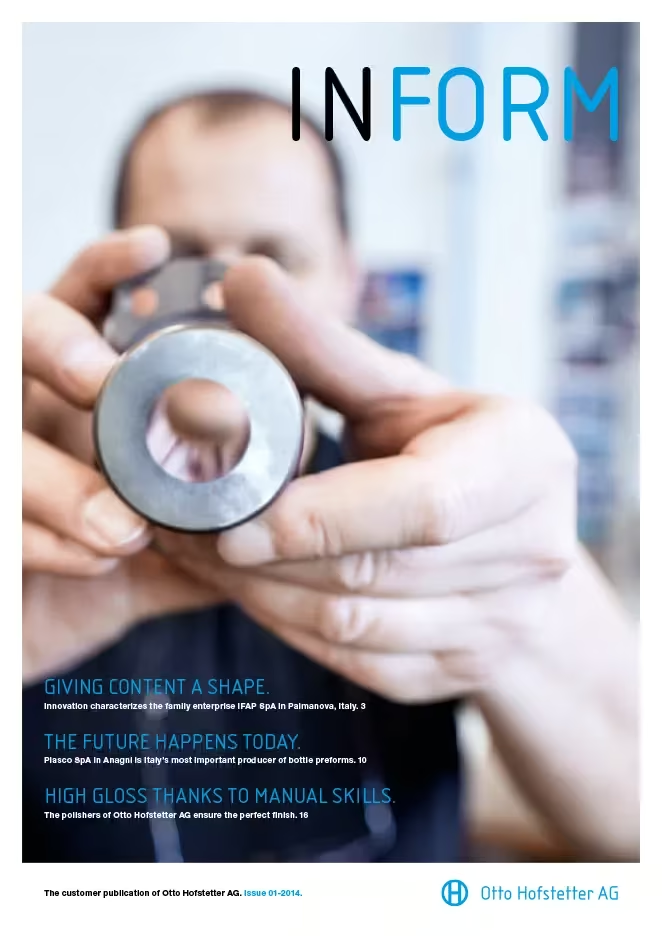
Issue 2014-1
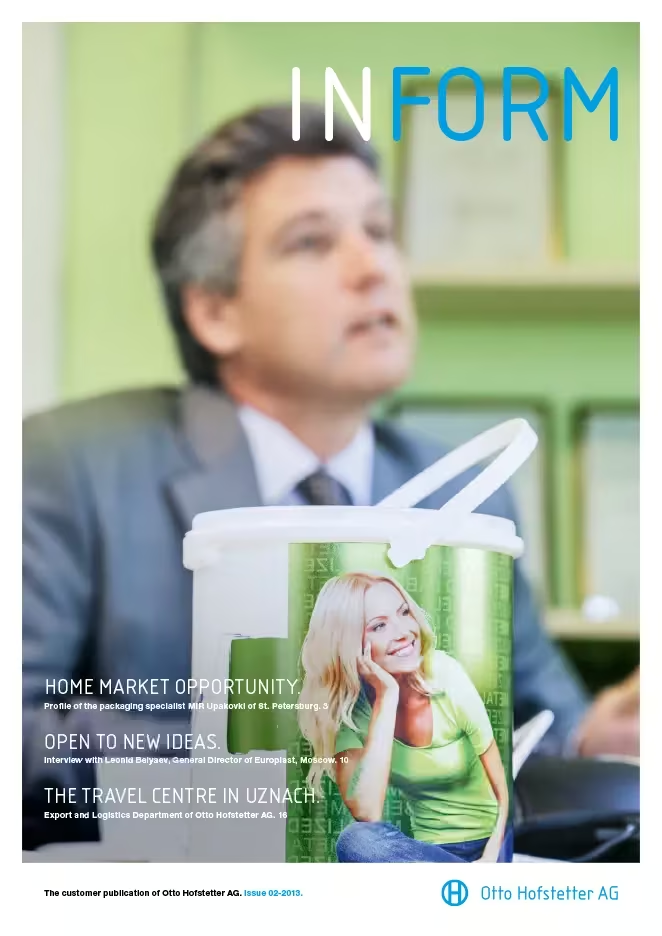
Issue 2013-2
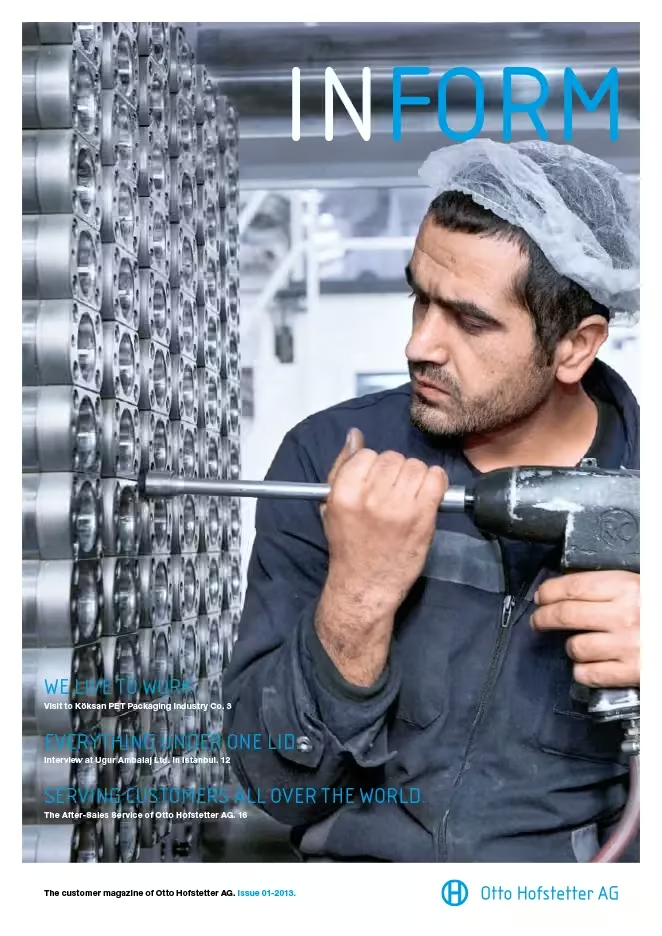
Issue 2013-1
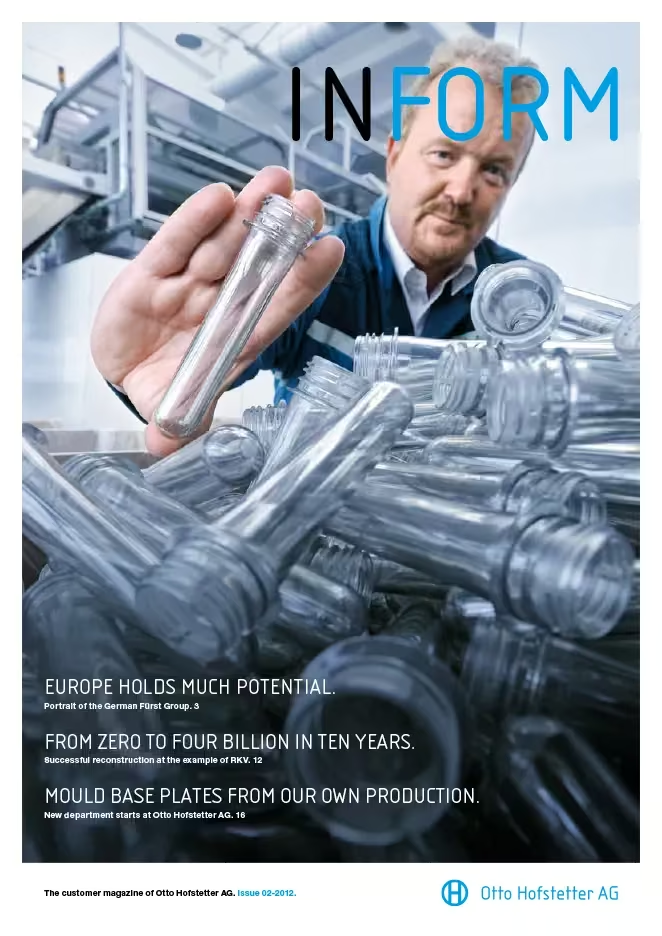
Issue 2012-2
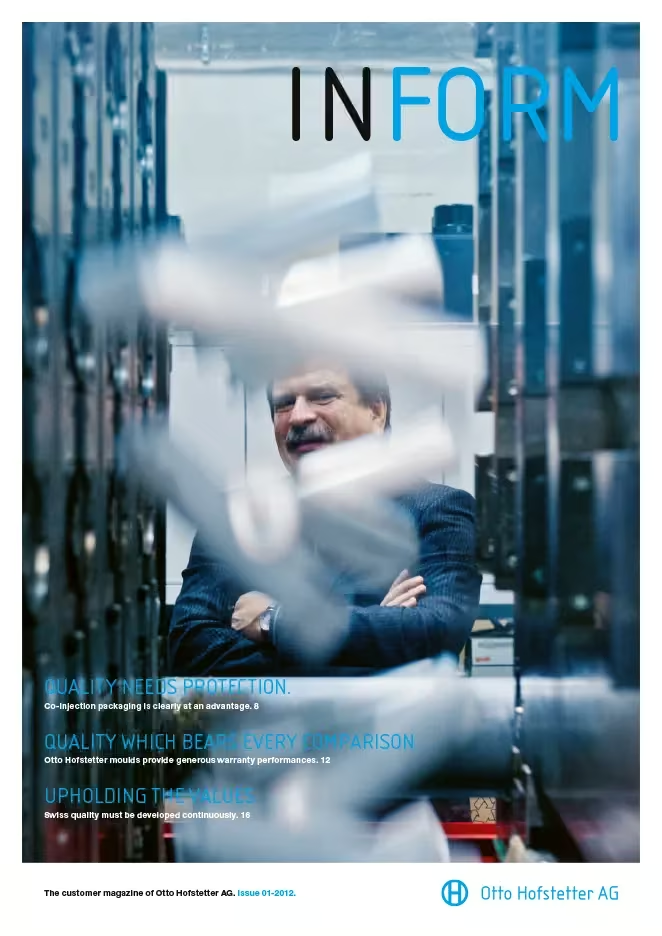
Issue 2012-1
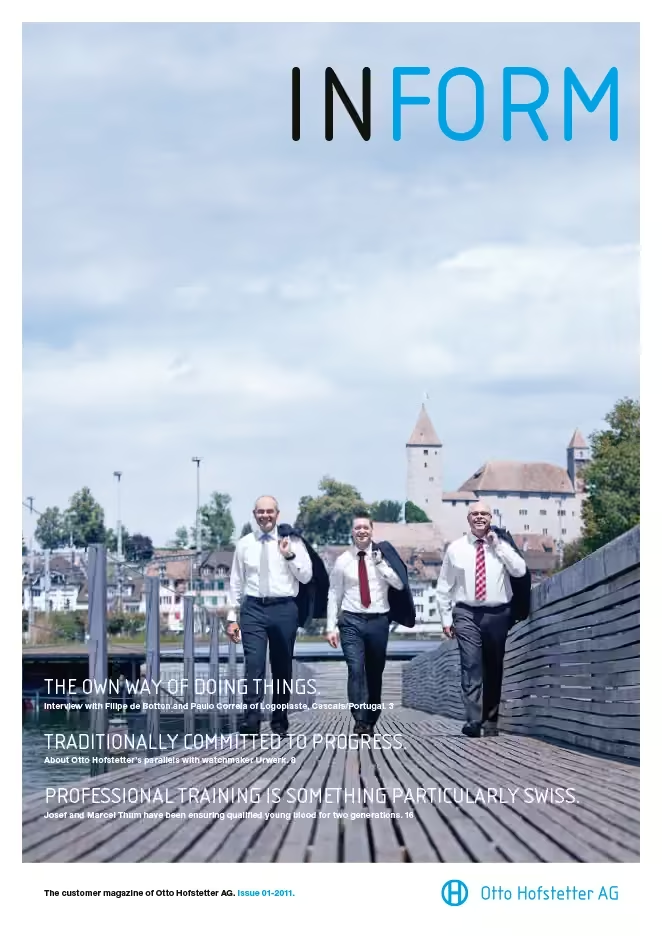
Issue 2011
Haven't you found what you were looking for?
Contact us, and we’ll be happy to assist you.